$100,000 wasted with each new home built
21 Jul 2015, Featured, Industry News
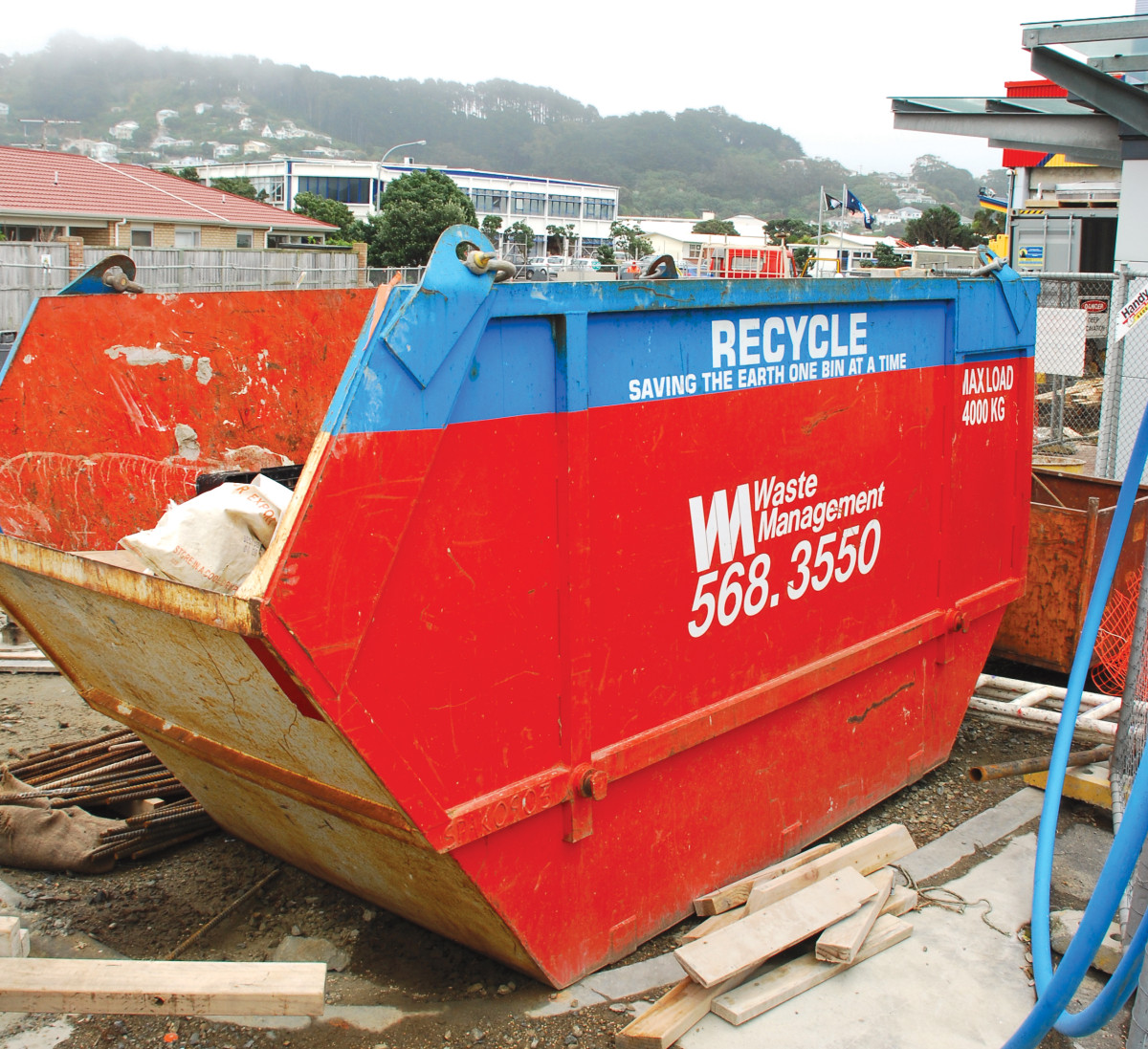
The Centre for the Urban Built Environment (Cube) at the Auckland University of Technology claims wasted resources are costing the city’s new home owners an average of more than $100,000
Cube’s numbers are based on the average house price, including section, of $828,000. Senior research fellow Jeff Seadon said that $31,000 worth of materials and $74,000 in labour are being wasted and that introducing mandatory skill levels on site would bring those figures down.
However, Registered Master Builders chief executive David Kelly – who hasn’t seen the report – said that while skill levels are part of the problem, other aspects are often outside of a builder’s control.
“Good design and planning are critical,” said Mr Kelly. “Using standardised sheets of jib, for instance, reduces both waste material and time, because they don’t have to be cut.
“For builders, it’s important to think about the flow of work on site prior to starting a build, and hire contractors accordingly.”
Inspections take time
Mr Kelly said that because there are more than 60 consenting authorities across the country, each with their own system, inspection delays can contribute significantly to wasted time, particularly for franchise builders.
“Builders often have to sit around and wait for inspections,” he said. “What the industry is saying generally, is that a consistent system would add hugely to the ability to plan, because everyone will know what is required from the design stage through to a build’s completion.”
In the same vein, during PlaceMakers cross-country seminars, LBP registrar Paul Hobbs offered advice on
inspection delays.
“Different councils have different lead times for inspections, so keep an eye on how they’re tracking to reduce downtime,” he said.
Buyer beware!
Mr Kelly acknowledged the quality of builders and sub-contractors was also a factor, and said it is up to customers and main contractors to do their due diligence.
“History has shown us in New Zealand that, when there is a lot of work on, there is pressure on resources and people come into the industry who aren’t necessarily top-notch,” he said. “Main contractors need to make sure they employ staff they trust to perform quality work.”
He said homeowners also needed to do their homework and should avoid picking based purely on price, to ensure they end up with a quality builder.
Lean manufacturing
Mr Kelly said while it was impossible to achieve zero waste on site, a number of industry players are working hard on ways to minimise waste.
“A number of big firms are looking at what is called lean manufacturing, which is about really efficient design and build processes,” he said. “If you can standardise a lot of the build process, you can achieve quality results just through repetition. When everything’s different, you have to constantly reinvent solutions.”
He said it was encouraging that the industry was taking the issue seriously, and that there was a lot of work aimed specifically at how to increase efficiency on site.
Register to earn LBP Points Sign in