Changes to H1 in works
26 Feb 2025, Industry News, News
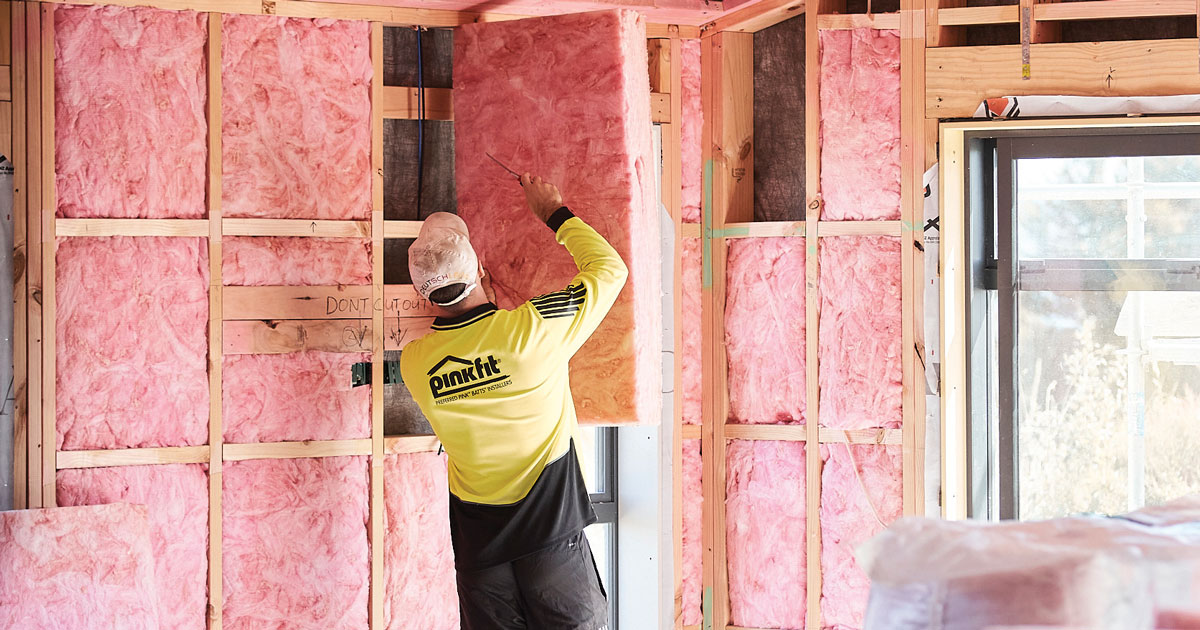
The Government is proposing ‘commonsense changes’ to H1 insulation standards designed to bring down the cost of home building. Suggested changes include removing the option to use the schedule method for calculating whether a building meets H1 requirements, adjusting minimum possible R-values for building elements and more
Building and Construction Minister Chris Penk said the changes will reduce the upfront cost of building while maintaining “robust energy efficiency standards.”
“We know from a social investment point of view that Kiwis do much better when they have access to affordable, insulated, secure housing. However, building costs have increased by more than 40% since 2019, with devastating consequences for Kiwis locked out of affordable housing.
That’s why […] I instructed MBIE to review the recently implemented H1 energy efficiency standards to ensure that compliance costs were not unreasonable and were well balanced with the health and efficiency gains.” At the time, concerns were also raised over whether increased insulation in the warmer parts of the country were appropriate or making housing too hot.
Revealing review
Since Penk’s request, MBIE has liaised with key building and construction stakeholders to review the current scheme and develop proposed changes to the H1 requirements. It was clear that, in general, stakeholders supported the current H1 settings and expressed the following views:
• Using the calculation or modelling compliance methods usually results in better outcomes compared to the schedule method.
• Any changes should be based on evidence. Assessment of costs and benefits should consider both upfront costs and long-term benefits. This includes energy efficiency improvements and the health and wellbeing benefits of warmer and drier buildings.
• Industry has made significant investments to meet the current H1 settings. Reversing them is unlikely to reduce upfront costs due to the sunk costs of these investments.
• Insulation does not cause overheating. Overheating is caused by poor design. It would be advantageous for the sector to collectively put more effort into providing education for designers to avoid overheating and internal moisture issues.
• MBIE should also consider updating the Building Code to help address overheating and internal moisture risks.
MBIE also engaged with the sector and commissioned further research and cost estimates for providing current insulation levels in new houses.
Compliance method matters
BRANZ’s cost-benefit analysis suggests that meeting the current H1 insulation requirements for housing and small buildings can be cost-effective and beneficial overall, and that the long-term energy efficiency benefits outweigh the additional upfront costs. However, the balance between costs and benefits depends on the compliance method that is used – using the calculation or modelling methods achieves the highest benefit-to-cost ratio overall. When using the calculation method, cost savings of between $3,712 to $9,565 can be achieved and, when using the modelling method, between $2,318 to $15,071. This is because the calculation and modelling methods enable people to adjust the insulation levels of different building elements to optimise a building’s overall energy performance in the most cost-effective way.
Overheating overblown
BRANZ also assessed whether the current H1 insulation requirements are creating overheating and internal moisture risks in housing. The research confirmed that housing overheating is not simply caused by insulation, rather it is a combination of design factors, such as sun heat gains during the day, window shading, heat absorption properties of building materials, as well as ventilation and building orientation. BRANZ’s analysis also shows that the current H1 settings are not increasing internal moisture risks in buildings.
Proposed change 1 – remove the schedule method
The proposal includes an option to remove the schedule method, which is one of three methods that can currently be used to see if a building meets Building Code requirements under the H1 Energy Efficiency Clause. The rationale is that “the schedule method may lead to higher upfront costs and less cost-effective construction than the more flexible calculation and modelling methods.” This is because these methods provide flexibility that enables the use of different, often lower insulation levels (R-values) than the schedule method. Therefore, it helps reduce upfront costs as well as improving the overall cost-effectiveness of the insulation in a building. However, because the schedule method is touted as the most simple to use for designers, and the easiest to establish compliance for with Building Consent Authorities (BCAs), it will likely require upskilling and create more work for designers and BCAs. The BRANZ analysis also shows that it would lead to higher energy use, meaning increased running costs and carbon emissions, because the calculation and modelling methods often enable compliance with less insulation than the schedule method. However, BRANZ suggests the estimated costs from this additional energy use – $53 to $236 per year when using the calculation method and $27 to $351 per year using the modelling method – are relatively modest in comparison to the savings in build costs.
Proposed change 2 – adjust minimum possible R-values in the calculation method
The calculation method uses simple equations and allows a designer to customise the insulation levels between different building elements, as long as the overall performance is comparable to or better than the reference building, which is insulated in accordance with the schedule method. In practice, this means trading off between elements, with higher R-values than those calculated in the schedule method table applied for some elements, and lower R-values for others. However, under the current H1 requirements, there are limits. For instance, using the calculation method, the minimum R-value for a floor, wall or roof building element is 50% of the schedule method R-value for that element. The proposal is to adjust the minimum possible R-values for roofs and floors – not walls – and to specify them directly in a table instead of using a percentage of reference building R-values. The rationale is that industry feedback and recent BRANZ analysis suggest that the current minimum possible R-values for roof and floors in the calculation method are too restrictive, resulting in unnecessarily costly and complex construction in some buildings.
Current and proposed new minimum R-values using the calculation method
*Based on 50% of the building element R-value in the reference building equations for respective climate zones.
A cited example of complex construction is the need for raised heel roof trusses to accommodate thicker insulation in some low-pitch or skillion roofs. A cited example of unnecessary cost is a slab-on-ground floor in a multi-storey house, where the only space that may be heated or cooled on the ground floor are the bottom of a stairwell and a small bathroom next to a large garage.
While designers are already able to use the modelling method (which does not have these minimum R-value requirements) in such situations, this is more time-consuming and requires access to modelling tools and specialist technical skills that not all designers have.
As a result, MBIE believes there will be less work for designers and BCAs when establishing compliance, as they will be able to use the calculation method when faced with unnecessarily costly and complex construction, rather than the more time-consuming and complex modelling method. Other impacts noted by MBIE include a minimal reduction in thermal comfort for building occupants, no significant change to energy usage, and no change to internal moisture risk.
Proposed change 3 – exempt embedded heating solely used in bathrooms from additional insulation
Building elements that are part of the thermal envelope and have embedded heating systems, such as floors with inbuilt underfloor heating, must meet certain minimum R-values. They apply irrespective of what compliance pathway is used and cannot be reduced.
These R-values are higher than the schedule and calculation method minimum R-values. This is to ensure that heated building elements have adequate thermal resistance to prevent excessive heat loss, enable efficient and effective operation of the embedded heating system, and limit heating energy use and costs.
Achieving the minimum R-values for heated building elements typically requires more insulation and upfront building costs. Where the embedded heating is used for general space heating across large parts of a building, these additional costs are generally outweighed by the ongoing energy cost savings from the additional insulation.
However, it is common for new homes to have underfloor or undertile heating solely in bathrooms, which accounts for just a small portion of a building’s floor. In this case, the additional costs required to achieve this may not be justified.
As such, MBIE is proposing to exempt buildings from the higher minimum R-values for heated building elements, where embedded heating systems are solely used in bathrooms.
Other proposed changes included in the consultation are:
- Updating requirements in the modelling method that are unclear or outdated, such as prescribing the use of the most recent NIWA weather files.
- Updating required building framing ratios to better meet insulation specifications
- Reducing the wall R-value in the theoretical reference building of the calculation and modelling methods from R2.0 to R1.6.
- Using overall internal dimensions to measure roofs, walls, and floors.
- Amending H1/AS1 and H1/VM1 to clarify requirements on how to apply NZS 4214.
- Amending H1/AS1 and H1/VM1 to clarify how a mixed-use building should be classified for H1 purposes.
- Amending slab-on-ground tables in H1/AS1 and H1/VM1 so they apply to more situations.
- Updating the look-up table for vertical windows and doors in H1/AS1 to include more common types of glazing.
- Updating H1/AS1 and H1/VM1 to remove obsolete provisions and update the latest editions of relevant resources.
Register to earn LBP Points Sign in