Framology a new way of framing
24 May 2024, Community & Sponsorship, News
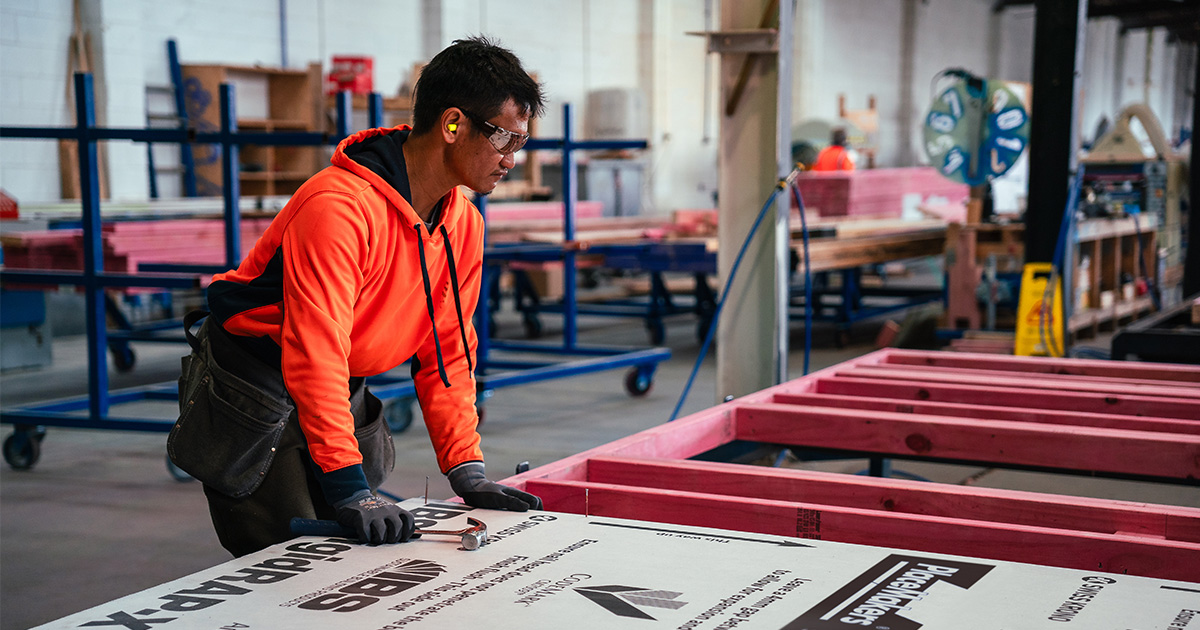
With wall framing now requiring a construction R-value of 2.0, PlaceMakers Frame and Truss is committed to helping builders achieve – and exceed – the new regulation in the best way possible. Under the banner of Framology, it has developed two innovative solutions
Timber is an excellent and easy-to-use sustainable building material that PlaceMakers Frame and Truss plants around New Zealand have been supplying to builders for decades. Due to thermal bridging, there is a direct correlation between the actual construction R-value and how much timber is within the wall framing. Thermal bridges are materials or elements that are better at conducting heat.
Better than baseline
When MBIE introduced the requirement that all walls in New Zealand, regardless of zone, achieve R2.0 as part of its updates to Building Code Clause H1 Energy Efficiency, it carried over the definition of construction R-value for a typical area of wall from the previous Standard to H1/AS1 2.1.4.3. This means that thermal bridging due to studs, nogs/dwangs, top plates and bottom plates is taken into account, but thermal bridging due to lintels, sills, the additional studs that support them, and studs at corners and junctions, is not.
In a bid to better understand the actual timber to exterior wall framing ratio – including all timber – BRANZ and Beacon Pathways conducted a study. Released in 2020, it found the actual percentage was between 24% and 57%, with an average of 34%, when accounting for all timber within the wall frame.
To showcase the difference it makes when all timber is taken into account, BRANZ highlighted the following examples.
With a framing ratio of 43% (taking all timber into account), using R2.0 insulation in 90mm framing will only achieve an actual R-value of R1.44, and using R2.8 insulation will only achieve an actual R-value of R1.57.
With a framing ratio of 23% (taking all timber into account), using R2.0 insulation in 90mm framing will only achieve an actual R-value of R1.79, and using R2.8 insulation will only just achieve an actual R-value of R2.0.
As a result, many in the industry are suggesting using 140mm framing, which is deeper and can therefore accommodate thicker insulation with a higher product R-value – a solution the Framology team doesn’t believe is necessary.
Team Framology steps in
As National Technical Resource Manager Pete Hammond succinctly put it: “While using 140mm framing in external walls allows space for a higher performing insulation, it increases the cost and complexity. We wanted to find a solution for those who would still prefer to use 90mm framing, but also want to work toward achieving an actual R-value of R2.0 when taking all timber into account – not just the timber specified to be included in the construction R-value required in H1.
“I strongly believe this is possible in most instances.”
To help designers, builders and homeowners achieve this, the Framology team developed a two-step solution. Firstly, the amount of timber stipulated in a build is reported through the Timber Percentage Report, and secondly Framology has developed a building method that will reduce that amount. That method is nog’less sheathed framing.
The first of its kind in the market, PlaceMakers Framology Timber Percentage Report is used to determine the timber to wall area percentage. Based on the design that would normally be provided to PlaceMakers Frame and Truss for a quote, the report includes:
- Average timber percentage ALL – includes all timber in a build.
- Average timber percentage ALL w/o NOGS – includes all timber in a build without nogs (also known as dwangs in parts of New Zealand).
- Average timber percentage SELECT – includes only wall timber that H1 Acceptable Solution counts such as studs, nogs and plates, but not lintels and corner studs, etc.
Released in September 2023, more than 1,000 reports have already been provided to designers and builders.
Nog’less is more
The second step in the process – nog’less sheathed framing – was released to market in February. Several builds are already under way and one has been completed (see image). While the concept of reducing or removing nogs – the horizontal blocking pieces used between the wall studs – isn’t new, PlaceMakers Frame and Truss is the first large-scale operation to execute the concept.
“Removing nogging that’s not needed reduces the overall timber percentage by about 4%, which can make quite a difference to thermal bridging,” says Pete.
“Then we sheath it with RigidRAP-XT®, an insulated rigid air barrier with a product R-value of R0.41. Combined with an R2.8 insulation product, this approach will achieve a true R2.0 construction value in 90mm framing in most scenarios.”
While PlaceMakers promotes using RigidRAP-XT®, the nog’less framing can be sheathed with other rigid air barriers, such as EcoPly, upon request, or can even be provided to site as standalone framing – it just requires careful handling.
A long time coming
People have been questioning the purpose of nogs/dwangs for decades. The first study suggesting that the practice of nogging was unnecessary was published by MJ Collins in 1974, followed by several BRANZ studies (1991, 1998 and 2011) and BRANZ guidance (2020).
Most other countries eliminated the practice decades years ago, when kiln-dried timber became commonplace, but Kiwis have
held onto the traditional building method. In its BRANZ Beacon Pathways study, BRANZ suggested the additional framing could have a number of origins including:
- Design requirements added to one area of regulations without consideration of other areas.
- Building in higher wind zones and how wind zone requirements are calculated and applied by local authorities and design and building professionals.
- Cladding trends, such as increasing popularity of vertical profiles, which require 400mm or 480mm nog/dwang spacing depending on wind zone.
- Changing styles and preferences.
- More multi-storey dwellings.
- Less than optimal placement of windows, doors and openings at the design stage. (In some instances, shifting a window anywhere from a few millimetres to 300 mm to one side could negate the need for additional framing.)
“People have been questioning the purpose of nogging for more than 40 years, so it’s about time we applied that tried and tested logic,” says Pete. “We look forward to helping our customers build houses without unnecessary thermal bridges that compromise energy efficiency.”
Talk to your account manager to see if Framology’s Nog’less Sheathed Framing is right for your client’s project.
Register to earn LBP Points Sign in