Concerns mount over scarcity of building supplies
02 Sep 2021, News
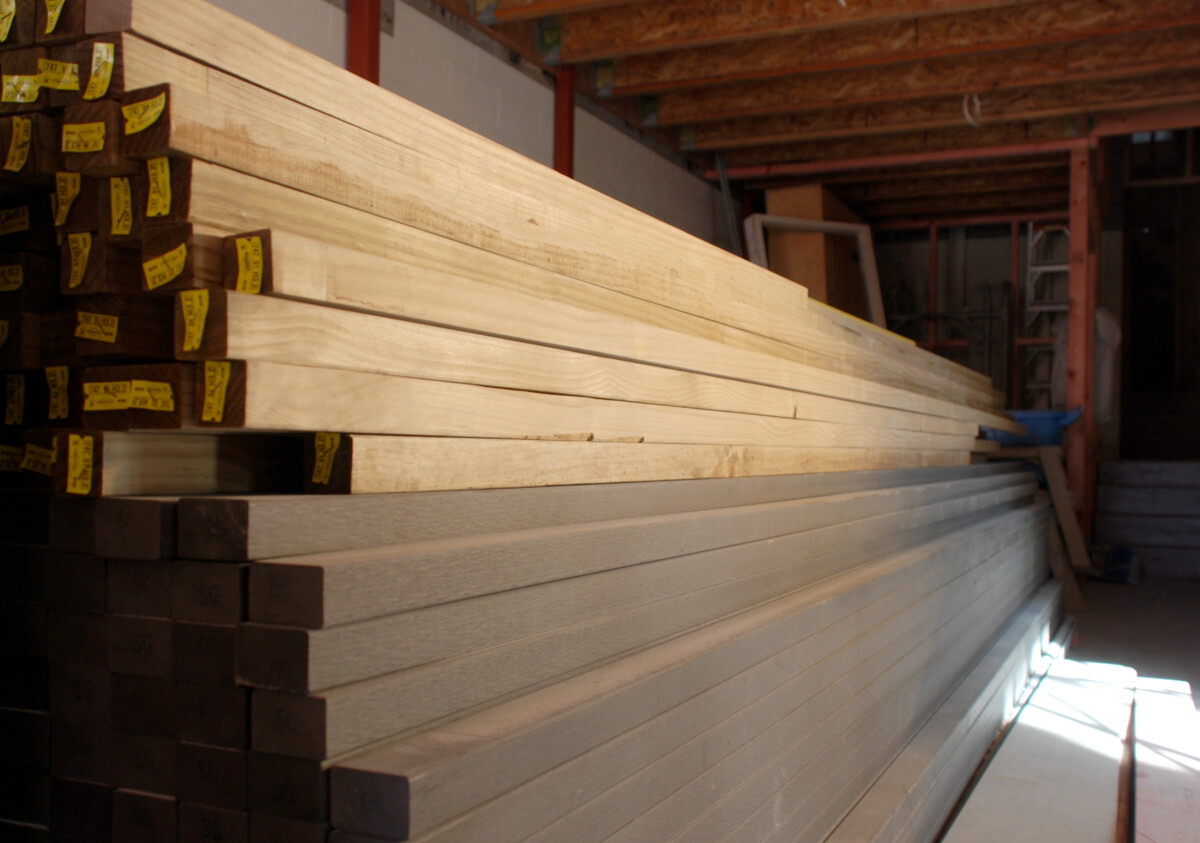
Some commentators are calling for NZ to increase the amount of building supplies manufactured here, as numerous spokespeople and reports paint a grim picture about building supplies in NZ
Wellington architect Bruce Welsh believes building supplies are scarcer than they’ve ever been.
“From talking to people across the industry, I have heard of issues like merchant shelves almost empty of timber framing, plywood and engineered timber beams, concrete can take weeks to arrive and window joinery takes months,” the owner of Rimu Architects told Under Construction.
“Imported items have even longer delays due to shipping, container supply and transport hold ups. Claddings from James Hardie can now take 18 weeks if you are lucky enough to get your order in on time, and some major contractors will not quote for work involving structural steel due to the uncertainty of supply and pricing. Electrical components and whiteware can also be months out, if even available.”
Welsh said he’s been told prices can change within a day, up or down by 20%.
“Materials shortages, labour shortages, supply delays and increased costs are now all part of the everyday experience of those in the building industry.”
One solution touted by some commentators is to boost the amount of materials created in New Zealand.
Cost of shortages and shipping
This comes on top of May’s NZ Property Focus report from ANZ which found “significant capacity pressure” in the construction sector – with materials shortages a big part of this. “It’s become difficult and expensive to find the raw materials needed to build houses,” the report said. “COVID has disrupted international supply chains and driven up the price of raw materials such as timber, and this is adding both time and cost to building projects.”
This has boosted the cost of house builds significantly and delayed new house builds, adding to a shortfall of 70,000 houses, the report said. New houses are indisputably increasing in build costs, with Stats NZ reporting a 4.6% jump in new housing building costs in the June 2021 quarter – the highest jump since 1987.
New Zealand Building Industry Federation chief executive Julien Leys, meanwhile, said New Zealand is no longer included on global shipping and building supply routes, with supplies getting only as far as Australia. Leys told news site Supply Management in early August that he had has spoken to one NZ company spending as much as $65,000 per week on shipping costs to ensure security of supply.
“We have to find a way to manufacture things ourselves and fill those supply gaps,” Leys said.
Maritime Union of New Zealand national secretary Craig Harrison also spoke to Supply Management, saying NZ needed to boost its own shipping capacity to lower dependence on overseas carriers. Harrison said ongoing congestion and delays in New Zealand’s supply chain mean there is no indication when this situation might end.
Pacifecon business manager Trina Farr added that the construction sector was seeing increased demand from local firms.
“Some companies are ordering stock as soon as they’ve won a job, despite the project not commencing for some time. Some businesses have completely reviewed their purchasing and project management systems,” she said.
Julien Leys told Stuff that four factors were working together to push supply down and costs up:
- NZ trying to build 40,000 new homes to meet the housing shortfall.
- People doing more renovations thanks to Covid stimulus cash.
- Historic under-investment in timber mill infrastructure,
- More overseas demand for New Zealand wood.
Leys estimated some building projects could have eight-month delays.
The shortage of one of the most sought-after materials, timber, is showing up in many metrics. Stats NZ data indicates export prices for logs rose 9.1% over the March quarter to reach the highest prices on record and in the first two months of 2021, exports in forestry products increased by 27%.
Meanwhile Prefab NZ chief executive Scott Fisher told Newsroom in July that the US and China hoovering up Kiwi timber and logs, combined with shipping delays, has meant a perfect storm for “skyrocketing” prices of raw materials, leaving locals paying international prices for raw materials.
Register to earn LBP Points Sign in