Hands on for H1
22 May 2023, Learn, Prove Your Know How, Technical
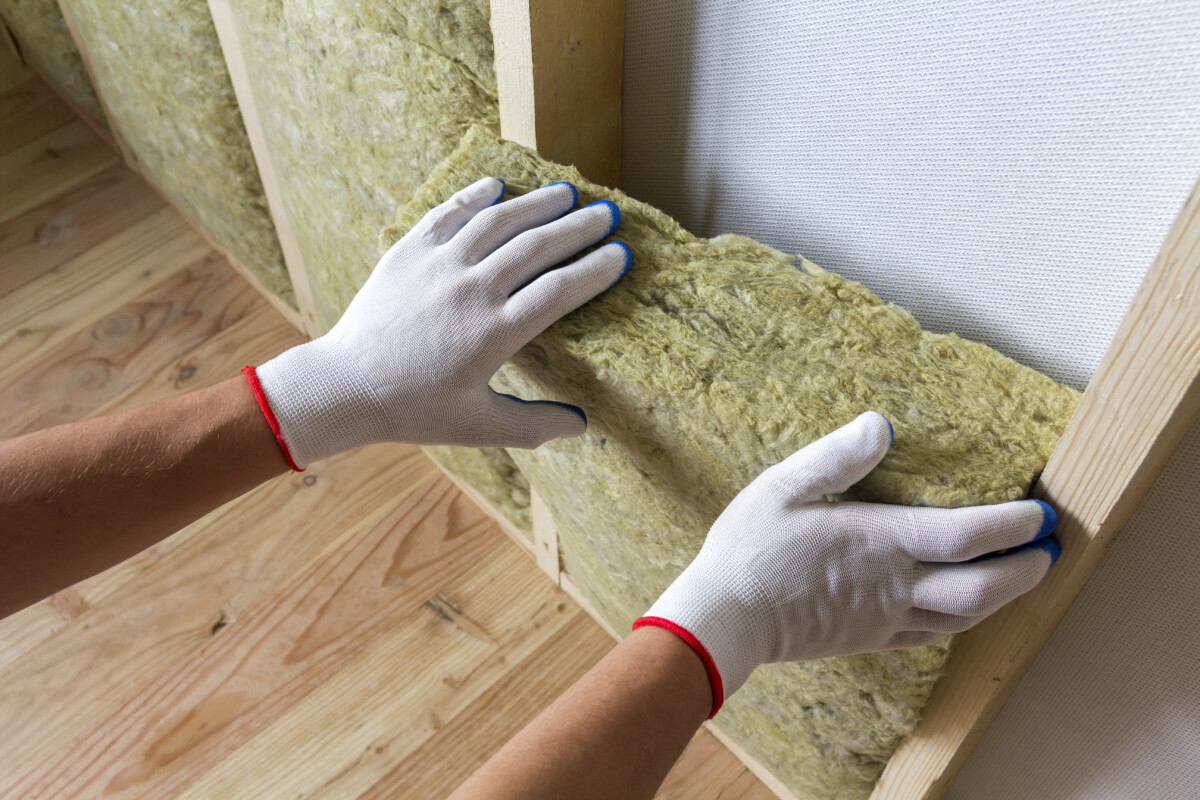
With decades of research into thermal insulation, structural strength, internal moisture and related topics, BRANZ is well placed to give practical advice about some recent questions we’ve heard around H1 compliance
There is nothing revolutionary in the building materials and techniques required to comply with the new Acceptable Solutions and Verification Methods for Building Code clause H1 Energy efficiency. Houses have been designed, consented and constructed this way in Aotearoa New Zealand for years. What is different is that the materials and techniques are being brought fully into mainstream construction.
Key principles to follow
This means that more than a few people will be doing things they haven’t done before. For any given project, following a few key principles will help:
- Choose the most appropriate compliance option for that project. Where using the schedule method seems fraught with difficulty, the calculation or modelling methods offer greater flexibility.
- Choose the right roof and wall framing options.
- Choose the right building materials or elements.
- Know where to find key information such as construction R-values.
- Know what’s not in the new H1 documents that you need to be aware of.
Choose the right compliance pathway
The schedule method in H1/AS1 has been very widely used in the past, but under the new requirements, the calculation or modelling methods may be a more practical way to meet the needs of a particular project. In some cases, you may be able to choose between several compliance pathways.
With roofs, for example, using the schedule method of compliance, all roofs require a construction R-value of R6.6. If this is a challenge, say for a particular skillion roof, the calculation or modelling method could be used. These allow – with some limits – a lower R-value in the roof if the R-values of other building elements are increased to compensate.
Mixed use buildings over 300m2 that include housing and non-housing classified uses such as those with commercial spaces on the ground floor and residential above – multiple classified uses – may be consented using multiple pathways. The commercial space on the ground floor may be designed according to H1/AS2 or H1/VM2, and residential floors above may be designed according to H1/AS1 or H1/VM1.
Another interesting mixed-use situation is buildings that include industrial and non-industrial uses such as commercial. Here, only the non-industrial part of the building needs to meet the H1 Energy efficiency requirements. However, the total size of the building – the area of occupied space including the industrial part – determines whether to use H1/AS1 (VM1) or H1/AS2 (VM2). For example, for a large industrial warehouse with a small office, the small office would not be able to use H1/AS1 or H1/VM1 as the total area of occupied space of the entire building is over 300m2.
Choose the right framing options
90 x 45mm timber wall framing has been very widely used in New Zealand for a long time, and the new H1 allows this to continue as long as the framing ratio is less than 25%. But moving to 140mm wall framing allows space for a conventional insulation product of R4.0 rather than the R2.8, which is the maximum in 90mm walls. (With an R4.0 insulation product and 25% framing ratio, the construction R-value of the wall is R2.89.)
Using timber battens to frame a cavity for a secondary insulation layer to the internal face of the main wall framing is becoming more common. The 45 x 45mm – or similar – timber battens are spaced to suit the installation of insulation and mounting the interior lining. It is crucial to ensure that the interior wall lining is airtight to reduce the risk of moisture transfer. Wall bracing will need to be considered with this option. A secondary insulation layer can almost double wall construction R-value in some circumstances. (The BRANZ House insulation guide 6th edition has examples.)
A secondary layer of insulation is also a possibility with roofs.
Another way to achieve high insulation performance in a roof is using a raised heel (see Figure 1). This is a timber post incorporated at the outer edge of the roof truss between the top and bottom chords, increasing the heel height of the truss and therefore allowing a greater thickness of insulation to be installed. (For more choices, see H1 and sloping truss roof options in Build 191, pages 40–42.)
Choose the right building materials and elements
Industry suppliers have come up with a host of higher-performing materials and building elements to help with the new H1 compliance. Where the products that were used before no longer achieve the construction R-values required, new materials/elements will need to be specified.
These are some examples:
- There are high-performance thermal insulation products available such as rigid foams that have higher R-values for a given thickness. Although insulated glazing units (IGUs) have been used in mainstream residential construction for many years, they have very often had no thermal break in the frame, no thermally improved spacer, and just dry air in the space between the panes. Today, thermal breaks, thermally improved spacers, low-E coatings and argon gas can make considerable improvements in their performance.
- New products such as structural insulated panels (SIPs) may be a good option for some projects – they are already being used in residential construction here.
Find the right information
For roofs and walls, construction R-values can be calculated using NZS 4214:2006 Methods of determining the total thermal resistance of parts of buildings or looked up in the BRANZ House insulation guide.
For windows and glazed doors, you can use Appendix E in H1/AS1 (Table E.1.1.1 in H1/AS1 can only be used for housing), calculate their R-values using H1/VM1, or use proprietary software programs such as WINDOW or flixo. For skylights, Appendix E in H1/AS1 and H1/VM1 gives guidance (but not tables) for calculating construction R-values. The table for vertical windows cannot be used for skylights.
For slab floors, you can use the tables in Appendix F in H1/AS1 or calculate using Appendix F in H1/VM1. The BRANZ House insulation guide includes the same slab floors plus some additional ones. For example, it includes slab floors that have topper insulation on top of the slab. These additional scenarios are helpful for those that struggle to find a slab that achieves the required R-value within the H1/AS1 look-up tables.
For other floor types, including suspended floors, you can use the BRANZ House insulation guide or calculate using NZS 4214:2006.
What’s not in the new H1 documents
The new Acceptable Solutions and Verification Methods take a big step in the right direction in keeping our buildings warm, but they haven’t fully considered the risk of buildings overheating. (The need to consider overheating and tips for how to do this are briefly referred to in H1/AS1 section 2.3 – future Building Code changes are likely to address this in much more detail.) Overheating is a risk that BRANZ scientists are very aware of – in fact, several BRANZ research projects have found this is already a serious problem. Designers need to think carefully about reducing the risk of overheating and the increased energy costs and occupant discomfort this brings. Avoiding overheating requires careful attention to:
- Shade devices – particularly considering the northern and western side of houses.
- Ventilation – ideally cross-ventilation, but other types such as stack ventilation are also useful. Glazing – the size and location of windows and glazing specification, including the solar heat gain coefficient (see Solar heat gain coefficient for windows in Build 189, pages 36–37).
Another big concern of BRANZ scientists is internal moisture, especially the risks of moisture passing from the living areas in a house through to the wall assembly or roof space. Condensation in these areas can lead to mould, rot and corrosion, which can be bad for occupant health and material durability. BRANZ scientists have encountered this in several relatively new homes. The risk increases as our buildings become better insulated. It is crucial, therefore, for design and construction to be carried out in a way that stops moisture from living spaces passing through wall and ceiling linings – airtightness is a key parameter. H1/AS1 section 2.2 (comment 2) touches on this.
The gains are worth it
There is no doubt that the changes being introduced will be a challenge for practitioners who have in the past aimed for Building Code compliance on their project, without going much further. For example, the roof construction R-values are twice or more the previous requirements. The benefits in the changes are substantial too. MBIE modelling indicates that the new insulation requirements will reduce the heating energy requirements in
new homes by 30–50% depending on the housing type and climate zone. That’s an achievement the industry can be proud to be part of.
Other BRANZ resources to help with H1 compliance include:
- A suite of bulletins, including bulletins focused specifically on H1 and roofs, floors, windows and the calculation method.
- Schedule and calculation method tools.
- Previous webinars on the calculation method and windows, doors and skylights under H1. The online H1 Hub at www.branz.co.nz/energy-efficiency/h1-hub.
Find these resources by visiting www.branz.co.nz and typing H1 in the search box.
This article was first published in BRANZ’s Build 195 magazine. www.buildmagazine.co.nz. Words and image supplied by BRANZ.
Register to earn LBP Points Sign in
2 Comments
Leave a Reply
You must be logged in to post a comment.
a lot to remember
ok