Have you taken a SIP?
25 Jan 2024, Learn, Prove Your Know How, Technical
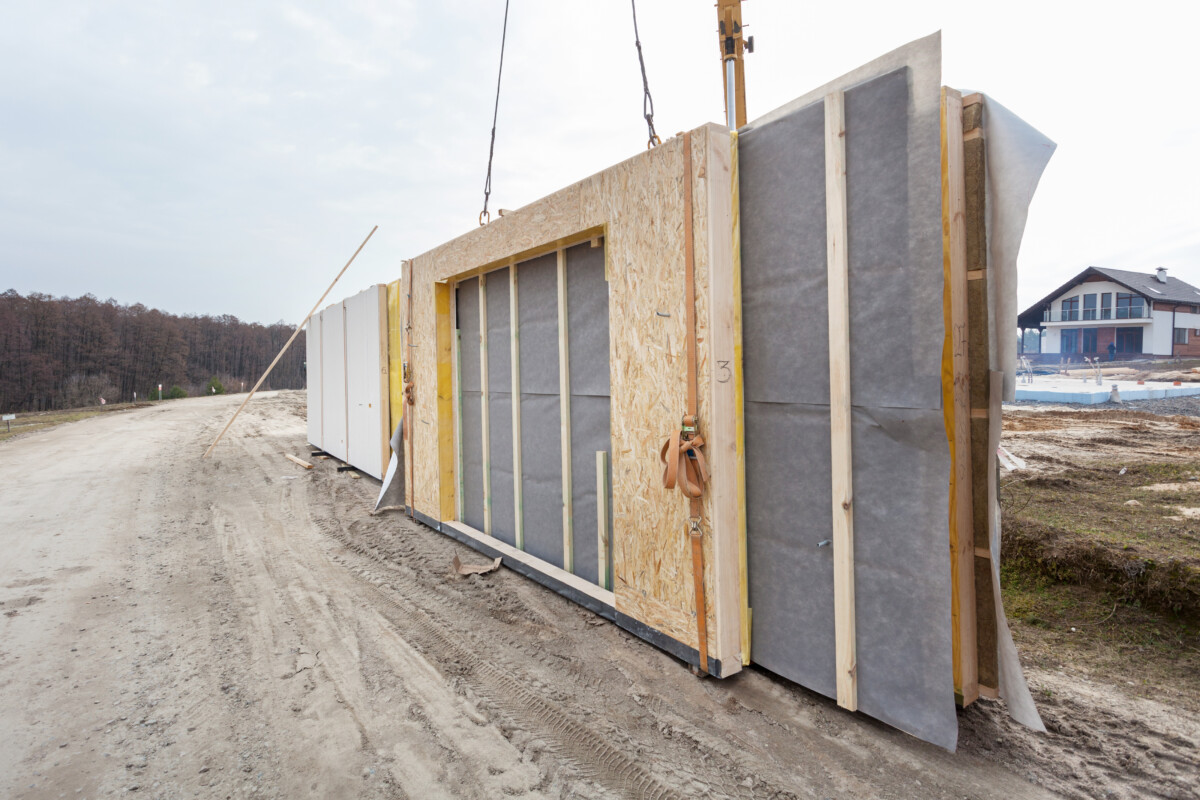
Structural insulated panels are relatively new to Aotearoa New Zealand residential buildings, but they have benefits in thermal performance and construction speed that are making them increasingly popular
Structural insulated panels (SIPs) themselves are not a new arrival. Think of a commercial cold store and steel-skinned panels with an insulating core probably come to mind. Those are SIPs, and that type has been around for decades. What is new is the expanding variety of skins and cores now available and the growing use of SIPs in home building.
What SIPs comprise
The SIPs used in homes are lightweight sandwich panels, typically made up of two high-density face layers bonded to a low-density cellular core. The face layers are usually:
- Engineered wood panels – oriented strand board is common.
- Cement board – including magnesium oxide (MgO) board made with an MgO cement, lightweight filler materials and glass fibre mesh reinforcing.
- Metal – lightweight steel or aluminium, which may be corrugated for strength and stiffness.
The core provides insulation and structural support by distributing load between the face layers. Common core materials include:
- Expanded polystyrene (EPS).
- Extruded polystyrene (XPS).
- Polyurethane (PUR).
- Polyisocyanurate (PIR).
The core may be bonded with adhesive to face layers – the usual process for polystyrene – or may self-adhere if it is injected between face panels as a liquid, which is most common with PUR or PIR.
SIPs are manufactured here, imported from overseas or assembled here using overseas and/or local components. They are often proprietary products with their own design guides, engineering calculations and recommended construction methods.
Advantages and disadvantages
Construction with SIPs produces a high level of airtightness and higher thermal performance than can be achieved with 90mm timber-framed exterior walls (see the section on H1 below). Where SIPs are made into wall, floor, ceiling or roof sections off site and craned into place on site, construction can be faster than conventional materials and methods.
The main disadvantage is that SIPs often cost more than conventional building materials. This may be offset by lower labour costs if sitework
takes less time and lower operating costs where the SIPs have high thermal performance.
Building with SIPs
SIPs are available as panels 1.2m wide and 2.4m, 2.7m, 3m or 3.3m long (longer by special order). Panel thickness varies depending on the face layers and core, but panels around 100–120mm thick are common and up to 300mm or more is possible. Weight varies between products. One manufacturer indicates 20 kg/m². Another indicates 75kg for a 2.4 x 1.2m panel with engineered timber face layers.
SIPs can be used for structural and non-structural components. They can be supplied on pallets and installed one panel at a time on site or be prefabricated off site into wall, roof and floor sections with window and door openings cut out.
Panels with timber-based faces can be connected with timber or LVL splines (rectangular elements that fit into a groove), a foam block or mini-SIP splines and OSB splines (see Figure 1).
There are often solid timber or LVL members running along the top and bottom – the top and bottom plates (Figure 2 overleaf). These plates allow SIP walls to be connected to the roof, ceiling or floor systems, which may or may not be a SIP themselves. The bottom plate can be used as the connection between wall panels and the foundation.
Embedded framing that includes lintels is used as supports for loadbearing elements, including at window and door openings.
Cladding and lining
Some manufacturers recommend a cavity batten system for claddings. Some also recommend battens on the internal walls, providing a cavity for electrical wiring behind the plasterboard lining. With others, the face layer can be used as the interior wall surface, either left exposed, painted or plaster skimmed and painted.
Wiring and plumbing
While some SIP systems run cables (or conduits) through a cavity between the SIP and the interior lining, others have chases precut in the core. With EPS cores, conduit or sheathing is required to prevent contact between cables and polystyrene.
Some manufacturers cut plumbing chases through the core, but many recommend that plumbing pipes are not run through the core.
Building Code compliance
SIPS are not currently included in Acceptable Solutions or Verification Methods, so Building Code compliance must use an Alternative Solution. For clauses such as B1, this requires an engineering assessment. Many SIP suppliers provide engineering calculations – project-specific engineering assessment is not required where products are used within scope.
Some SIP products have CodeMark or BRANZ Appraisal certificates.
B1 Structure and B2 Durability
The structural performance of SIP systems – the interaction between the outer skins and perimeter timber framing members – is similar to a timber-framed wall with plywood cladding. Local designers of SIP houses sometimes use NZS 3604:2011 Timber-framed buildings. Bracing ratings for wall systems used with NZS 3604:2011 can only be determined following the P21 test method.
BRANZ has tested the seismic performance of SIPs, funded by EQC and the Building Research Levy. Tested systems showed suitable energy dissipation, ductility, strength and stiffness for prescriptive and specific engineered wall bracing designs. Damage during cyclic
loading was less for the SIPs than most of the more commonly used bracing systems.
Under clause B2, SIP wall, roof or floor sections must have a minimum durability of 50 years.
C Protection from fire
In all current fire compliance documents, there are specific reaction-to-fire requirements for building systems that include foamed plastic or combustible insulation. All SIPs that include these products are subject to these requirements.
Acceptable Solution C/AS1 can be applied to low-rise stand-alone or multi-unit dwellings, where each unit is independent of all other units (classified as risk group SH). C/AS1 requires that wall systems that include foamed plastics or combustible insulation (which would apply to SIPs with a foamed plastic core) must achieve a Group Number of not more than 3. There are no other surface lining requirements in C/AS1 for the SH risk group. SIPs used in locations requiring a fire separation (such as inter-tenancy walls) or for external walls close to a boundary may also require a 30-minute fire resistance rating in SH buildings.
In dwellings in New Zealand, plasterboard encapsulation is often used as a means of achieving adequate fire resistance.
H1 Energy efficiency
The thermal performance of SIPs depends on component material and thickness. Manufacturers claim R-values of around R2.3 – R2.8 for 100–115mm thick panels with a standard EPS core to as much as R9.0 for panels over 300mm wide with EPS that includes graphite.
The airtightness of 888 SIP buildings means that SIP manufacturers often recommend mechanical ventilation such as heat recovery ventilation.
This article was first published in BRANZ’s Build 198 magazine. www.buildmagazine.co.nz. Words supplied by BRANZ.
Register to earn LBP Points Sign in
4 Comments
Leave a Reply
You must be logged in to post a comment.
Good
not seen these yet
Haven’t used this system, seems good
Good article