Interview with an inspector (Part I)
18 Jul 2017, Featured, Industry News, LBP & Regulation
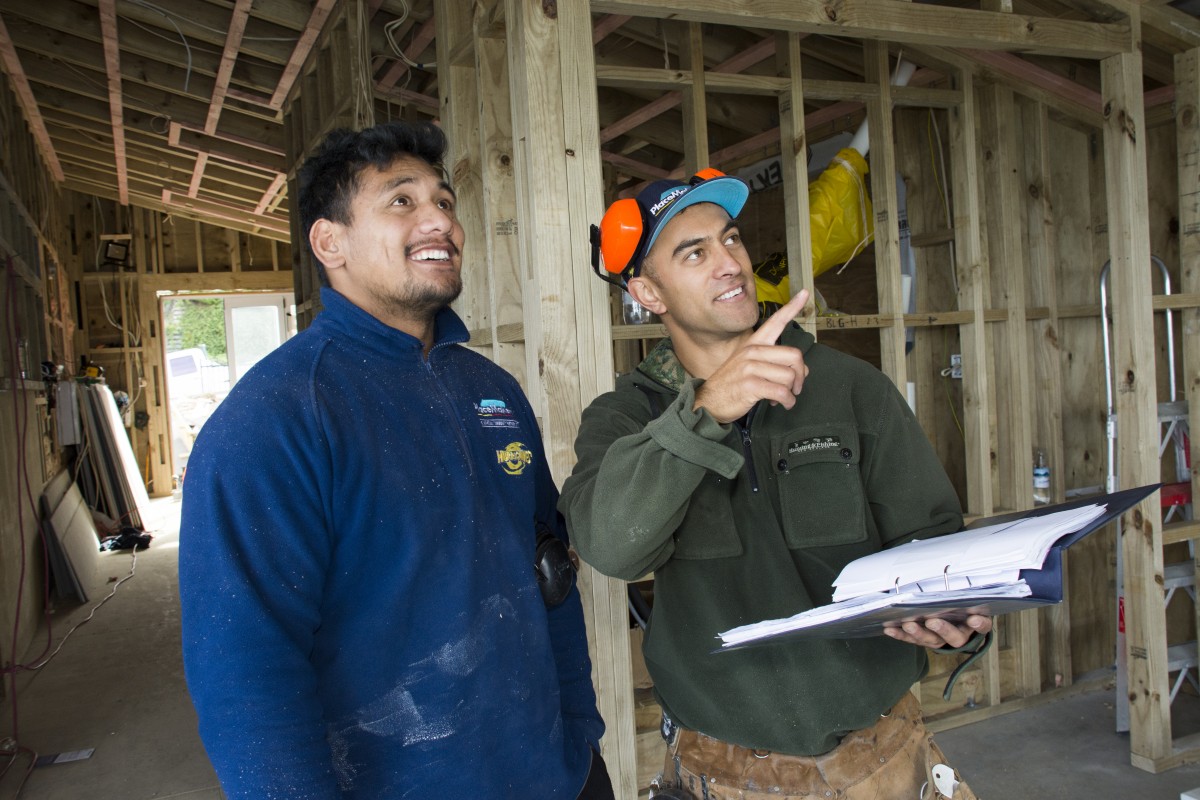
Building inspections are an essential part of the building process, so Under Construction spoke to Auckland Council inspections manager Jeff Fahrensohn to get a view from the other side
The average new house under construction can face up to 12 or more inspections throughout the build process, and Jeff says that, at each stage, missing paperwork is one of the most common reasons for a fail.
“There is a lot of paperwork required now. I’d say it has increased ten-fold compared to several years ago. I think there’s an element of builders relying on the council to point out to them what paperwork is needed and when. We don’t mind that approach, because we do understand that builders and project managers don’t always have time to sift through all the paperwork they need – given the pressure everyone in the industry is under at the moment.
“However, it does slow down the whole process by creating churn at the back end, which can delay the issuance of a Code Compliance Certificate. When a builder or project manager sends in the missing paperwork, it’s not always received by the same inspector. It means whoever receives it has to start from scratch trying to match what was sent in to what was requested.”
Full steam ahead
Jeff says that the past two years have been the busiest he’s seen in Auckland since becoming an inspector in 1996.
“We have a team of around 140 inspectors completing up to 1,000 inspections a day. We used to pride ourselves on offering next-day inspections, but we’re just too busy for that to be practical now.
Our wait times are at around three days at the moment, which I think is still pretty good!”
While the boom continues to apply pressure across all aspects of Auckland’s building industry, Jeff is pleased to note that pass rates are coming back to pre-boom levels.
“The quality is definitely getting better. If you go back to February 2015, probably 40% of all our inspections were failing and now it’s around 25%,” he says. “We’re finding people are taking a lot more time in terms of quality and I think that’s in part thanks to people having adjusted to the amount of work that’s on at the moment and recent industry changes.
“Failure rates consistently increase when new legislation or tweaks to the building code are introduced, which happens constantly.”
The pass rate for follow-up inspections is in the high 90s, which Jeff says is evidence of builders learning from their previous mistakes, which he credits as another reason for improving pass rates.
General tips and tricks
Jeff suggests builders looking to improve their inspection process should:
- Ensure they’re ready for an inspection by going through their own checks, which can help pick up little things such as missing bolts or top plate connectors.
- Learn from failures, identify knowledge gaps and fill them as soon as they can.
- Not be afraid to ask questions and enter into dialogue with inspectors to make the most of their knowledge.
Part 2 of the article will be featured in the next print edition.
Register to earn LBP Points Sign in