Is H1 causing a headache?
24 May 2024, Builders business, News
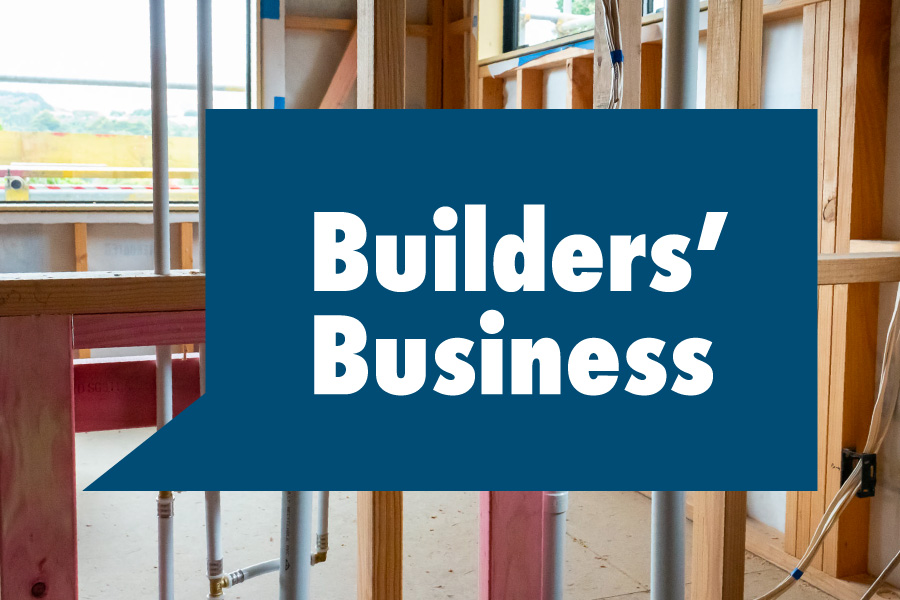
Builders’ Business is a column by builders for builders. Its objective is to provide a forum, particularly for small business operators, in which to share knowledge, experience, tips and ideas
Q. What have been the implications of the new H1 insulation requirements?
Firm: Quality Construction
Interviewee: Dan Albert
Role: Director
Location: Wellington
Staff: 5
We were applying the insulation systems prescribed by the latest H1 regulation update long before they came into force. Even when H1 updates weren’t required by law, when we explained the benefits to clients, they never objected.
We were a bit concerned about the availability of insulation materials once the regulation came into effect but found our suppliers had it all sorted.
Materials have driven overall costs up slightly but, on the labour side, we haven’t had to charge any more for installation. The biggest cost increase has actually been accommodating the increased bulk, both in deliveries and on-site storage, for insulation.
Another unforeseen consequence is the increase in packaging waste. We don’t have ways to recycle the soft plastic packaging.
While the H1 regulations help the environment by reducing the cost and power requirements for heating and cooling homes, it has increased non-recyclable construction waste. That’s something we need to look at because it somewhat diminishes the overall environmental goals that the new regulation is designed to achieve.
Firm: Versatile
Interviewee: Brad South
Role: Director/Franchisee
Location: Invercargill
Staff: 8
Since the new insulation requirements came into force, we’ve experienced an increase in build cost. However, I find putting an exact figure on it difficult because different insulation products have increased by different amounts.
For example, using thermally broken windows adds about 10% and, if you need to use a product such as Hot Edge on your slab, that can add 10% as well. Other increases may not be as much.
On the labour and build-time front, I haven’t seen much of an increase. However, if we need to increase the thickness of the wall insulation because we can’t meet the required R-value from floor, window and ceiling insulation, we might increase the framing from 90/45 to 140/45, and that comes with additional labour costs.
Before the change, I was concerned that supply may not cope with demand, but I haven’t experienced any shortages. It’s also been a smooth process for us to go from the old regulations to the new ones, as it was well communicated, especially through PlaceMakers, and we’ve known about them for some time.
Firm: Gray Brothers
Interviewee: Mark Ward
Role: Co-owner/Director
Location: Dunedin
Staff: 13
I’ve found the transition to the new H1 insulation standards to be fairly easy. I haven’t experienced any supply concerns and, in terms of it adding additional cost to a job, it hasn’t done so at a level that’s especially noticeable.
One thing that has helped keep build costs at around the same level is the reduction in price for some materials, as more supply has hit the market.
For example, 4×2 timber has come down by about $1 per metre, so it’s swings and roundabouts. I think the easing of Covid supply shortages has helped the industry a lot and we’ve seen prices go down as a result.
While the new R-values haven’t had a big impact on the business, I’d say the trend to place more of an administrative burden on builders has had a big impact.
For example, five years ago I had 18 staff and employed one office worker to manage it all, but now we have three in the office and less on the tools. Getting work over the line seems to be a more painful process than ever!
Register to earn LBP Points Sign in