Managing internal moisture
17 Mar 2023, Learn, Prove Your Know How, Technical
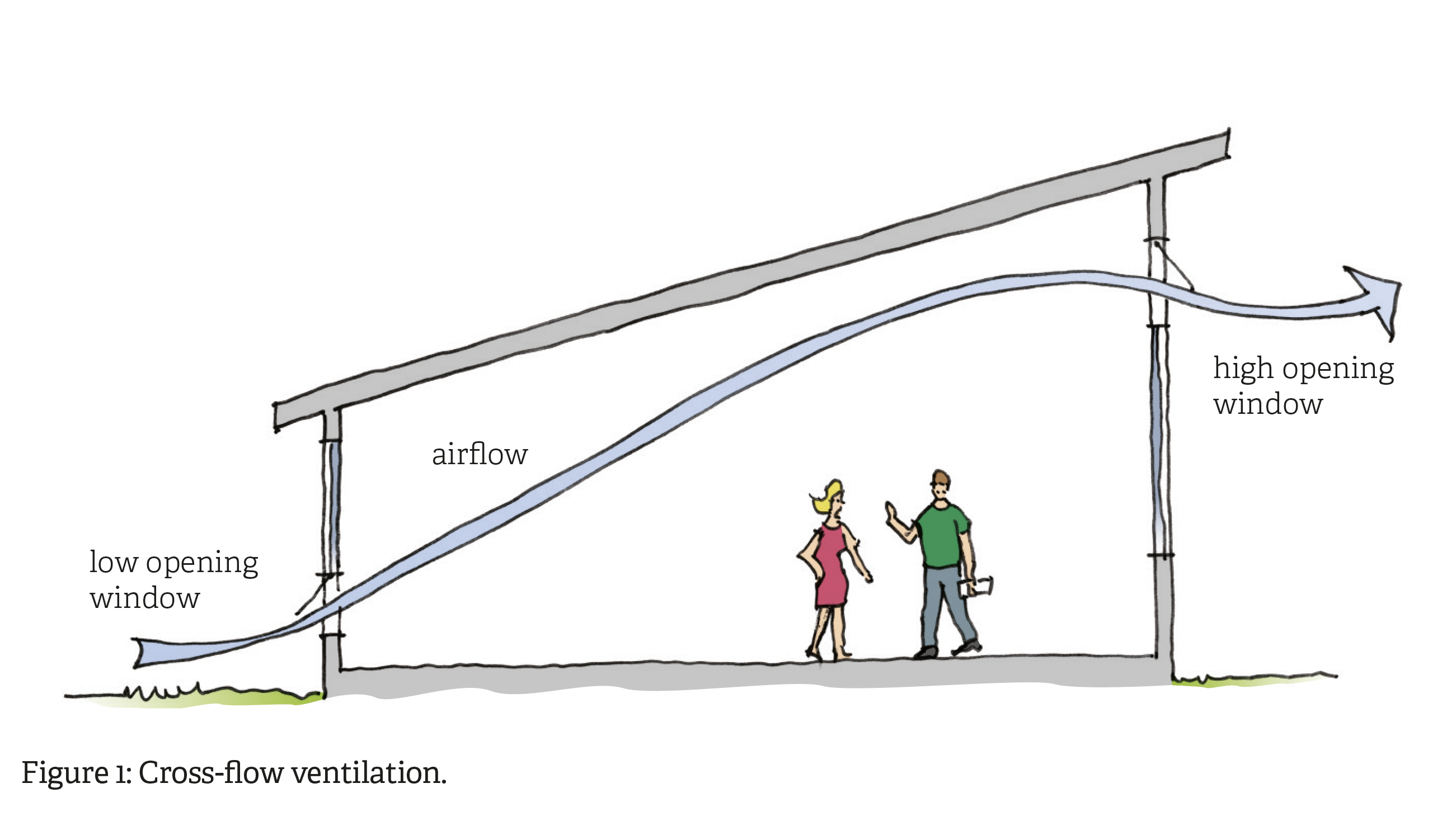
High levels of indoor moisture are one of the major contributors to unhealthy homes. Indicators include condensation on windows and hard surfaces such as mirrors and tiles, mould and mildew growth on ceilings, walls and curtains, and a musty, stale smell
It can be both harmful to health and damaging to interior spaces and can be challenging to manage effectively – indoor moisture is produced constantly and from many sources.
Sources of indoor moisture
The main sources of internal moisture in New Zealand homes come from occupants’ daily activities such as:
- Cooking.
- Washing.
- Showering or bathing.
- Drying clothes indoors.
- Unflued gas heating.
- Respiration.
Other sources can include construction moisture, leaks from internal or external sources and subfloor moisture infiltration. This article deals with indoor moisture control arising from occupants’ activities.
Activities such as cooking, washing and showering or bathing cannot be eliminated but can be managed by good ventilation at source.
Moisture generated from unflued gas heaters and drying clothes indoors can and should be completely eliminated. An unflued gas heater can be replaced with another heating source such as electric or flued gas heating, and clothes should not be dried indoors except in a space with good cross-flow ventilation.
Ventilation
Good ventilation – the process of supplying and removing air to control air quality – is the key to effective management of internal moisture. It is most effective when moisture is removed at its source.
Ventilation can be:
- Passive (natural) ventilation.
- Mechanical ventilation.
Passive ventilation
Passive ventilation occurs when windows are opened.
New Zealand Building Code clause G4 Ventilation requires that all occupied spaces are ventilated. Acceptable Solution G4/AS1 1.2 states that natural ventilation must be achieved by providing an area of opening windows or other openings to the exterior that is at least 5% of the floor area of the space. This requirement cannot control the amount of moisture removed.
Cross-flow ventilation and stack ventilation
The effectiveness of passive ventilation can be increased by cross-flow ventilation or stack ventilation.
Cross-flow ventilation is achieved by opening windows on more than one external wall of the room, allowing a cross-flow of air (Figure 1). It occurs because of differential air pressures on either side of a building that pull air through the interior space.
Stack ventilation occurs where there are low-level and high-level windows that provide an open path through which air can flow such as opening clerestory windows or in two-storey construction (Figure 2). It is caused because of warm indoor air rising and exiting through openings higher up in the building – resulting in air being drawn up through the space.
Trickle ventilation
Trickle ventilation provides continuous passive ventilation while maintaining security with two-setting window fasteners or grilles or mesh-covered openings in window sashes. Both allow a continuous flow of fresh air into the room. The two-setting window fasteners allow the window to be opened a very small degree and still maintain security, while grilles or openings in the window sashes means there is some ventilation when the window is closed.
The openings can generally be closed off by a sliding cover, and some trickle ventilators have automated opening and closing. Trickle ventilation is available as an optional extra in new aluminium joinery and can be installed into existing aluminium and timber windows.
Infiltration
Infiltration – uncontrolled air movement through gaps and openings in the building envelope – typically occurs because of differential air pressure between the interior and the exterior.
It occurs readily in older homes that are more draughty, but infiltration cannot be regarded as a means of providing ventilation in new homes, which have become increasingly airtight with the aim to reduce infiltration to an acceptable level. Therefore, alternative means to introduce fresh air into new buildings must be employed.
Mechanical ventilation
Under clause G4, buildings must have a means of collecting and removing cooking fumes and odours and moisture from washing and bathing. G4/AS1 1.2.5 states that household and accommodation units with mechanical extract fans (for intermittent operation) are to have flow rates of at least 25 L/sec for showers and baths and 50 L/sec for cooktops.
Mechanical extractor fans in kitchens typically consist of a rangehood over the stove or cooktop or a downdraft extractor system adjacent to the cooktop. Some cooktops also include an integrated downdraft ventilation system. Rangehoods and downdraft extractor systems discharge to the exterior through ducting.
Extractor fans in bathrooms may be either wall or window-installed fans that discharge directly to the exterior, or ceiling-mounted extractor fans that are typically ducted through the roof space to discharge through the roof, a soffit or an external wall.
Ducted mechanical ventilation systems must discharge to the exterior of the building, not into a ceiling or subfloor space. Ducting from separate extract fans must not be combined or shared. If they are, ductwork dampers must be installed.
Whole-house ventilation systems
Fresh air can be brought into new, airtight homes with the installation of a whole-house ventilation system. These systems basically consist of:
- Fans to move air in and out.
- Ducting.
- Intake grilles and outlet diffusers
Two generic systems available are:
- Balanced (heat recovery) systems.
- Supply (positive pressure) systems.
Balanced systems
A balanced heat recovery system is a ducted system consisting of two fans – one to draw air in from outside and one to remove stale internal air to the outside. An air-to-air heat exchanger, generally installed in a roof space, recovers heat from the outgoing air before it is discharged to the exterior (Figures 3 and 4).
The recovered heat is transferred to the incoming air before it is pumped into the indoor spaces. By recovering some of the heat from the outgoing air, less heating is required to maintain a comfortable indoor air temperature.
Supply systems
A supply or positive pressure system brings air inside to create a slight positive pressure inside that forces stale, indoor air out through gaps and air leakage paths (Figure 5). For this system to be effective, the supply airflow rate must be higher than the leakage airflow rate.
While supply ventilation systems are generally designed to run continuously, some systems will vary the air-change rate depending on the temperature difference between outside and inside.
This can potentially mean insufficient fresh air being brought inside during colder weather and result in inadequate ventilation and high moisture loads.
Solar ventilation air preheating systems
Solar ventilation air preheating systems use solar energy to preheat fresh supply air that is drawn through solar panels before being pumped to the interior. As they use the sun’s heat to warm the air, they can be efficient to run, and the solar cells can also be used to power the fans. However, these systems can be expensive to install and only operate efficiently when the sun is shining.
Improving ventilation during renovations
Improving ventilation must be considered when planning renovation work.
A whole-house ventilation system may be too difficult or costly to install into an existing house, but kitchen and bathroom renovations should include installing mechanical ventilation systems.
Other means of improving ventilation such as installing additional windows to provide more window opening area or to facilitate cross-flow ventilation should also be considered.
This article was first published in BRANZ’s Build 193 magazine. www.buildmagazine.co.nz. Words supplied by BRANZ.
Register to earn LBP Points Sign in
1 Comment
Leave a Reply
You must be logged in to post a comment.
can be confusing