PACE AND SCALE!
04 Apr 2021, Builders business, News
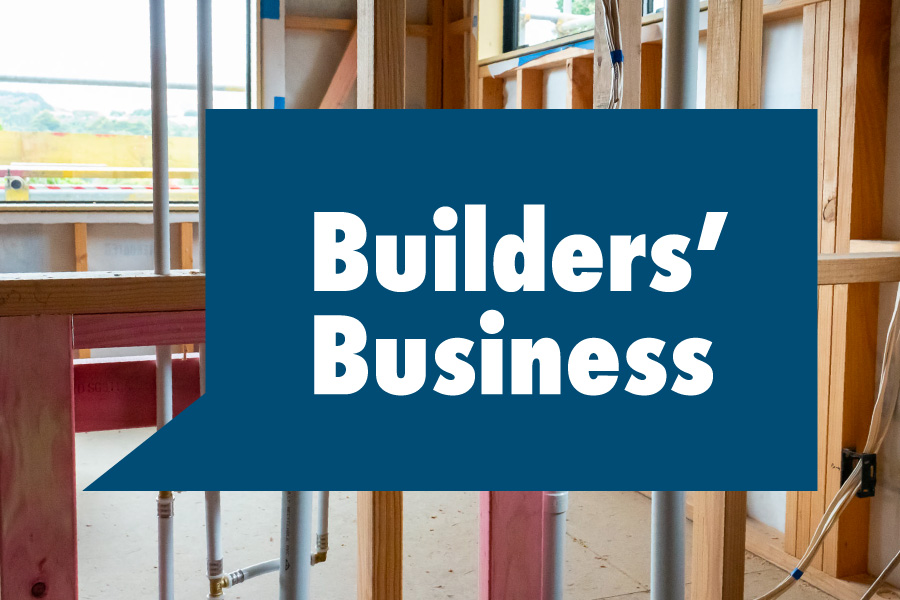
Builders’ Business is a column by builders for builders. Its objective is to provide a forum, particularly for small business operators, in which to share knowledge, experience, tips and ideas
Q. What could be done to solve the undersupply of houses?
Firm: Hamr Home
Interviewee: Richard Warwick
Role: Director
Location: Whitianga
Staff: 10
Most of our work here in Whitianga is new builds, mainly for locals, as well as for people moving to live here from the cities. I think a big part of resolving the supply issue is bringing down the cost of new builds. Without changes to the cost, a new home is pretty far out of reach for would-be buyers of new homes. I’m hopeful the 3repeal and replacement of the RMA will free up land and make that part of the house cheaper. Of course, it would be great if building supplies were cheaper too!
Another option to bring cost down is building more duplex and terraced homes. They’re common in places like the UK. I know they are growing in popularity in the cities here, but we haven’t seen them in Whitianga yet.
Modern expectations of houses also contribute to the cost. When I grew up, my parents had 100m2 universal home. It was a simple three-bedroom home with one bathroom and a garage. But these days, expectations are far greater for a first home, and, because the land is so much more expensive now, it’s a hard sell to put a cheap house on a pricey piece of land.
Speeding up the consenting process would make a difference too. It’s not uncommon for that to take two months – certainly not the 20 days it’s meant to take, because the council wait until the 19th day, then send out a request for more information. That is frustrating!
Firm: Universal Homes
Interviewee: Sunilp Parsad
Role: Project Director
Location: Auckland
Staff: 64
We are at the face of trying to solve the undersupply of houses – we’ve got 1,300 units going into the Westgate development in Auckland. It’s a big project with lots of pieces to fit together, which directly relates to the country’s ability to build new housing at scale.
Not everything has gone as smoothly as it could to help us supply these dwellings. I know the government keeps talking about investing in ‘shovel-ready’ projects. You can’t get more shovel ready than this project – we are under way, but facing a council that initially agreed to support the development with funding of infrastructure, like roading and parking, but now says they can’t fund that. This seems like a good place for central government to step in.
Having said that, from where I’m sitting, the government is doing a lot overall. It looks from here like it has put housing at top of its list.
Of course, with such a big project, there are a lot of council consents to get through. But we are fortunate to be part of a ‘qualified partner group’, which is an Auckland City Council programme where they have taken all the big group home builders and provided a streamlined consenting process. To the council’s credit, it’s been working well – we meet with them every month, give them a heads up about what consents we’ll apply for and they update us on how existing consents are going.
I hear some smaller builders are struggling to get supplies, as a result of Covid-19. We are fortunate not to have had that issue. With a multi-year project like this, we warn our suppliers a long time in advance about our needs and, so far, I have not seen any problems with our supplies.
Overall, I think our project is an example of how New Zealand can solve the housing supply issue.
Firm: TMT Construction
Interviewee: Tim Moriarty
Role: Director/builder
Location: Christchurch
Staff: 4
I would say the main issue is there is a shortage of skilled labour. A long-term fix for this would be to make apprenticeships free – to fully subsidise employers for the apprentices’ training every year. That would produce a lot more apprentices, which would be for the long-term benefit of the country.
I’d also like to see LBPs given more responsibility for what we can sign off. Currently we carry a lot of liability but we can’t actually do much without it being signed off by someone else.
If we could sort out shipping issues, so we could get rid of the material shortages we are currently experiencing, that would make a difference too.
Register to earn LBP Points Sign in