Importance of non-structural elements
03 Jan 2017, Featured, Industry News
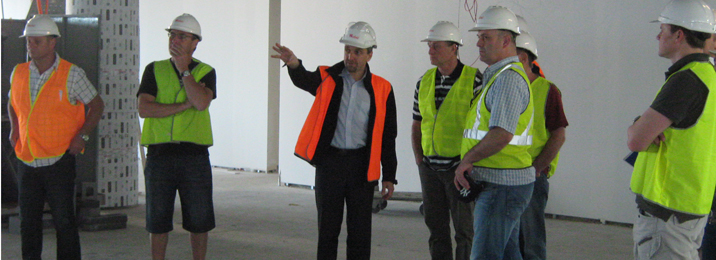
Prompted by recent seismic activity across the country, MBIE has issued two practice advisories detailing the importance of ensuring non-structural and secondary structural elements will perform as intended in an earthquake
Both the 2010 and 2011 Canterbury earthquakes and the 2013 Wellington shake highlighted many cases where elements not part of a building’s primary structure performed poorly, particularly in multi-storey buildings – a cause for concern, as they have the potential to cause injury and death.
As a result, the Ministry of Business, Innovation and Employment (MBIE) released two practice advisories to the building sector on non-structural elements and secondary structural elements in commercial buildings in November 2016. Building and Housing Minister Dr Nick Smith said the advisories would help to improve the safety and resilience of commercial buildings during earthquakes.
“Structural failures in buildings pose the greatest risk to people’s lives, but elements such as ceiling panels and ducting can also injure people and cause death. These failures are a major component of the post-earthquake repair cost that can significantly disrupt businesses and their staff while repairs take place,” said Dr Smith. “We are seeing too many examples of ceiling panels, ducting and features, such as hanging sculptures, failing in the Christchurch, Seddon and now Kaikoura earthquakes.
“Often these features are added after the building has had its Code Compliance Certificate (CCC) issued, without sufficient thought to the risks they pose in a seismic event. Particular care needs to be taken with those additions, which are sufficiently large to cause an injury or death.” An MBIE spokesperson said that irrespective of whether the work was done before or after a CCC is issued, it is up to individual councils to determine what is required when consenting and signing-off non-structural elements.
The spokesperson added that at all times, all building work must meet the Building Code and that building owners are obligated to ensure that requirement is met.
Non-structural elements
MBIE Practice Advisory 19: Improving earthquake performance of non-structural elements defines non-structural elements as building components not considered part of either the primary or secondary structural systems, such as:
- Mechanical and electrical plant.
- Ducting.
- Pipework.
- Cable trays.
- Suspended ceilings.
- Light non-load bearing partitions.
- Cladding systems, such as brick veneer.
Significant damage during the Canterbury earthquakes was caused by non-structural elements, such as ceilings and in-ceiling services, clashing as a result of insufficient clearance and/or stiffness incompatibilities.
When determining clearances for non-structural elements, use the clearance requirements of NZS 4219, where appropriate, or determine the clearance requirements taking into account construction tolerances, movements due to temperature change and the displacements that can arise from earthquake actions. An MBIE spokesperson said that there are a number of other common reasons non-structural elements can fail.
“Inadequate design, such as restraint systems that aren’t strong or stiff enough to resist the earthquake’s actions on the element, poor installation of the restraint system or no restraint system installed at all are all common causes of failure. Poor integration between the element, other elements and surrounding features is also another reason.
“However, even well-designed non-structural elements can fail, such as when nearby elements fall on them – which is why it’s important these types of risks are taken into account when they’re designed and installed.”
Secondary structural elements
MBIE Practice Advisory 20: Improving earthquake performance of secondary structural elements defines structural elements as building elements that are not part of either the primary lateral or primary gravity structural systems, but nevertheless are required to transfer inertial and vertical loads. Examples include: • Precast panels. • Curtain wall framing systems. • Heavy internal partitions. • Stairs. • Significant building services. • Large building ornaments. MBIE recommends that an engineer with suitable competency and qualifications in structural engineering be made responsible for the design and construction monitoring of secondary structural elements. The collapse of stairs and precast
cladding panels falling into the street are just two examples from the Canterbury and Wellington earthquakes of secondary structural elements failing. All secondary structural elements and their connections need to be designed to resist earthquakes, including differential movements of their attachment points. Secondary structural elements and their connections, both individually and as a part of a system, must also meet the applicable durability requirements of Building Code Clause B2 according to location and use. In many cases, this will be a minimum of 50 years.
Onsite collaboration key
Good communication between all parties, including building consent authorities, building owners, contractors, designers and engineers is required to ensure nonstructural building elements and systems perform adequately in an earthquake.
MBIE recommends that all parties engage in the design process early, to facilitate good design and help avoid problems later. Early coordination of non-structural systems also helps avoid conflicting specifications and work plans.
Careful detailing is required for nonstructural elements, so they can resist earthquake actions. Critical details, such as connections, restraints and, where required, flexible elements and/or separations should be identified and documented. There are generally two ways to detail non-structural elements and their connections:
1. Using details or proprietary systems verified as being compliant with the Building Code. These can be prescribed in Acceptable Solutions, standards or in literature developed by technical groups.
2. Using details which have been subject to specific engineering design. Details that result from a specific design should generally be the responsibility of an engineer with competency in structural engineering in the application of earthquake actions, such as a Chartered Professional Engineer (CPEng).
“This guidance is a clear reminder to architects, engineers, contractors, building owners and councils of their responsibilities under the Building Act, that they must make sure the risk of collapse of non-structural elements is low,” said Dr Smith. “The various players need to take a well-planned approach to make sure the design is coordinated and building elements are appropriately restrained.”
Liability determined case by case
An MBIE spokesperson said that the penalties facing a builder or contractor found to have incorrectly installed non-structural or secondary elements that result in death or injury would be dependent on the specific circumstances surrounding that case.
“If the builder or contractor suspected of being at fault is a Licensed Building Practitioner (LBP), they could face disciplinary action through the LBP Board following a complaint. Similarly, if a design issue was found to be the fault, the engineer responsible may face disciplinary action through IPENZ or the Chartered Professional Engineers Council.
“Depending on the circumstances, other courses of action might include the council issuing a ‘notice to fix’ against the building owner, or civil or criminal proceedings being laid against the builder or contractor suspected of being at fault. There may also be health and safety responsibilities under the Health and Safety at Work Act on the building owner for ensuring the safety of people who use their building.”
The full practice advisories can be found on MBIE’s website under Building Code compliance>B Stability>B1 Structure>Updates. They outline in more detail what is required of designers, contractors, building consent authorities and building owners. It is likely that these will have been updated since this was printed following investigations into the performance of commercial buildings during the 14 November Kaikoura earthquake.
Construction Monitoring
Onsite construction monitoring is crucial to verify that design details are built as intended. Particular attention should be applied to critical design information, such as fixing/ anchorage details and seismic clearances, such as clearances between non-load bearing panels and building columns.
Seismic gap details should be inspected periodically – during and after construction – to ensure that the gaps have not been partially or fully filled during construction or as a result of poor maintenance. This is especially important with egress stairs, because obstructing the seismic gap may restrict or prevent movement resulting in failure of the stairs and the loss of an escape route from the building
Register to earn LBP Points Sign in