HOW TO AVOID CONCRETE CRACKS
16 Jan 2020, Learn, Prove Your Know How, Technical
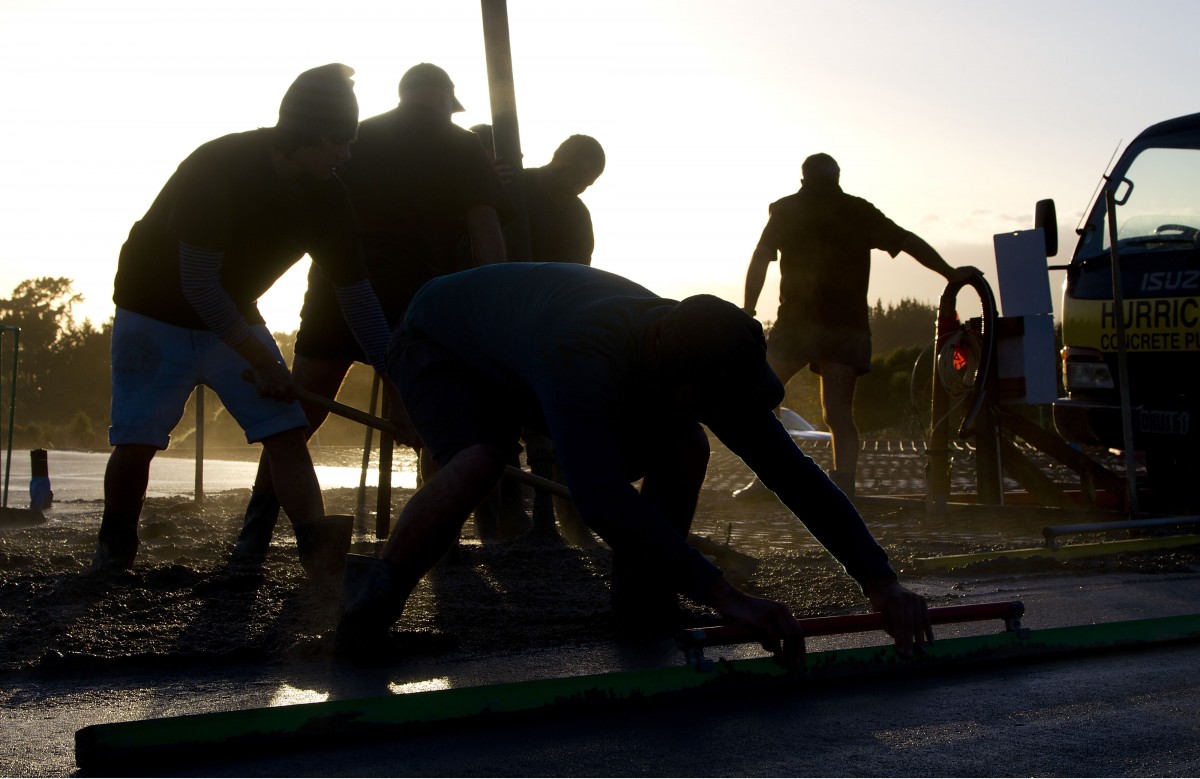
Depending where you are in the country, spring and summer can be high-risk periods for early-age concrete cracking. Higher daytime temperatures and dry winds, along with low evening temperatures, are a perfect recipe for the creation of cracks
If you want to minimise the time spent investigating and rectifying unwanted cracks in concrete, now is the time to understand the issues and the action you can take to avoid problems. The following looks at cracks which form in concrete after it has been placed but before it has set — when the concrete is in its plastic state.
Plastic cracking
The formation of cracks in concrete is somewhat inevitable and can form prior to the concrete setting, or after it is in its hardened state. During the setting stage, the moisture content of the concrete changes and water is given off, and hence the concrete shrinks. This shrinkage leads to a volume change, and as concrete has a low tensile strength, if this volume change is restrained, cracks will form. However, appropriate measures can entirely eliminate, or at the very least minimise, the formation of these unwanted cracks.
Cracks which form before the concrete has fully hardened (usually not less than about eight hours) are known as plastic cracks. Plastic cracking occurs as either shrinkage cracks or settlement cracks.
Plastic shrinkage cracks
Once concrete is in place, evaporation can only occur from the free surface. In the absence of appropriate precautions, and in unfavourable drying conditions, the rate of evaporation at the surface
can be greater than the rate with which water within the concrete can migrate to the surface to make good the loss. The highest risk weather for plastic shrinkage cracking is sunny and/or windy days with low humidity levels.
After concrete has been placed, vibrated, screeded and floated, it is left so the bleed water can rise to the surface. The slab cannot be finished until it is hard and the bleed water has evaporated. The bleed water will appear within about 15 minutes of placing and the slab is ready for finishing after several hours, depending on the concrete temperature. If the top surface is allowed to dry before final finishing, then plastic shrinkage cracking may occur.
The risk of plastic shrinkage occurring is greatest when:
- The temperature difference between the concrete and air temperature is large. In spring, this type of cracking can occur in an area exposed to the sun, while shaded concrete remains uncracked. Concrete exposed to the sun can be significantly hotter than the air temperature.
- Low bleed concrete mixes (eg, superplasticised mixes and/or mixes with high quantities of ultrafines) are used. The more concrete bleeds, the less likely it is that the surface will prematurely dry out. As such, greater precautions are required when using low bleed concrete mixes.
- There are low humidity days.
- There are high wind speeds.
What do plastic shrinkage cracks look like?
Usually, the cracks occur either while finishing or within 30 minutes to six hours of finishing, form without any regular pattern, and may range from 25mm to 2m in length. They may be straight or jagged and often intersect each other forming T junctions or acute angles. The cracks vary in width from a hairline to perhaps 3mm. Additionally, while they are surface-related, the cracks may extend deeper with subsequent drying of the slab.
How can plastic shrinkage cracking be avoided?
The most effective way to reduce the risk of plastic shrinkage cracking is to prevent rapid loss of moisture from the surface of the concrete.
Practices to achieve this are:
- Dampen the subgrade and formwork, while also ensuring any excess water is removed prior to placing concrete.
- In hot weather, lower the temperature of the fresh concrete by using cool aggregates if possible.
- Erect wind breaks to reduce wind velocity over the concrete surface.
- The use of polythene sheets on the top surface of the concrete will prevent both evaporation and air movement. These should be used with caution when trying to obtain a consistent colour to
the slab. - Use a proprietary evaporation retardant spray. These are inexpensive and provide a good degree of protection if used in accordance with the manufacturer’s instructions.
- Add polypropylene fibres to the concrete mix.
The use of polypropylene fibres works by evenly distributing many small reinforcement fibres throughout the mass of the concrete, in all directions, and intersecting any micro-cracking that occurs when the concrete shrinks.
Their physical properties are designed to match the properties (eg, the modulus of elasticity) of fresh concrete. Polypropylene fibres usually provide sufficient extra strength to prevent microcracks from widening and hence restrict the formation of plastic shrinkage cracking. Fibres are typically added at the batching plant and therefore their use requires planning. Your ready-mix concrete supplier will be able to advise on the appropriate dosage.
- Commence curing promptly after finishing is complete and ensure the surface is subject to continuous curing. Providing a fog mist spray to increase humidity above the concrete is a good means of achieving this, although it may be difficult to get a uniform application during windy conditions. It is important excess water is not added to the surface.
Plastic settlement cracks
Another form of cracking which occurs during the plastic stage of the concrete setting process is plastic settlement cracking.
Most concrete, after it is placed, bleeds. This means that water rises to the surface as the solid particles settle. The bleed water evaporates and there is a loss of total volume (ie, the concrete has settled’). If there is no restraint, the net result is simply a very slight lowering of the surface level. However, if there is something near the surface, such as a reinforcing bar, which restrains part of the concrete from settling while the concrete on either side continues to drop, there is potential for a crack to form over the restraining element.
Settlement cracks tend to follow a regular pattern, replicating the lines of restraint – usually the reinforcement or a change in section. Generally, the cracks are not deep, but, because they tend to follow and penetrate down to the reinforcement, they may reduce the durability of a structure.
Plastic settlement is affected by the following factors:
- Rate of bleeding from the concrete.
- Time over which settlement can take place – ie, the time before it sets.
- Depth of reinforcement relative to total thickness of the section.
- Size of reinforcement.
- Constituents of the mix.
- Slump.
Prevention of plastic settlement cracking
Plastic settlement cracks may be prevented, or rather closed, by revibrating the concrete after settlement is virtually complete and it has begun to set. However, the timing is critical and considerable experience is needed to know when that critical time is.
If revibration is done too early, more settlement could occur. If it is done too late, it could damage the bond between the concrete and reinforcement.
Other procedures which may help reduce plastic settlement cracking include using:
- Lower slump mixes.
- More cohesive mixes.
- An air entrainer to improve cohesiveness and reduce bleeding.
- Increasing cover to top bars.
With an understanding of the causes and precautions that can be taken to avoid plastic cracking, this common surface defect can be easily controlled.
The Information Bulletin IB 73 Cracking contains more information about concrete cracking and is available for download from www.concretenz.org.nz.
Concrete NZ is aligned with the New Zealand Concrete Contractors Association (NZCCA). To be a member of the NZCCA requires a high standard of knowledge and practical experience. To find out more visit www.nzconcretecontractors.org.nz
Register to earn LBP Points Sign in
2 Comments
Leave a Reply
You must be logged in to post a comment.
Good to know when working with concrete
sometimes it cant be avoided