Insulation implications
14 Oct 2022, Builders business, Feedback, News
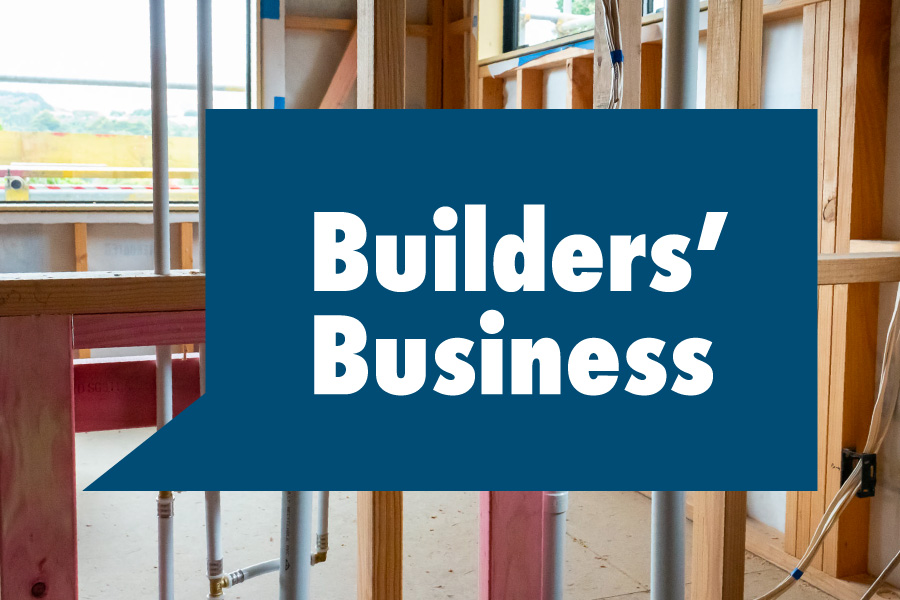
Builders’ Business is a column by builders for builders. Its objective is to provide a forum, particularly for small business operators, in which to share knowledge, experience, tips and ideas
Q. What do you think the implications of the new insulation requirements will be?
Firm: Versatile
Interviewee: Brad South
Role: Director/Franchisee
Location: Invercargill
Staff: 8
We will have to pass costs onto the customer, as increasing the amount of insulation in homes will make them more expensive to build. We’re not sure how much we’ll have to pass on yet, as there will be a few different factors we need to take into account, such as whether the insulation is in the slab, wall, windows or cladding.
I think another consequences will be that it’ll take longer to complete homes, as the subbies putting in insulation will have to do two layers instead of one. It was 90mm and now it’s 140mm, so there’s no way it won’t take longer – plus you’ll also need heavier frames, which will likely require a different approach for those handling the frames.
The other issue is supply and demand – will suppliers be able to keep up? If there’s a shortage, it’ll drive up price and that will result in higher house prices as well.
Firm: Sentinel Homes
Interviewee: Guy Richardson
Role: General Manager
Location: Nationwide
Staff: 100+
At the moment, we’re designing houses that are compliant with the current regulations, but we are notifying customers that if consents aren’t signed off by 1 May 2023, then a re-design may be required, especially in terms of ceiling insulation.
The new laws will add a significant extra layer of cost. For example, we currently receive one delivery of insulation bale per home and that will increase to two or three. So, in addition to purchasing more product, we’ll need a place to store them to avoid them being stolen.
Another big consequence for the industry is that working capital requirements for builders, installers and suppliers will increase. Right now, smaller installers, who operate out of a van, could be priced out of business because they’ll need to upgrade their vehicle to a truck and increase their working capital from $2,000-3,000 to $7,000-8,000. An unintended consequence of this could be less competition though smaller players dropping out. That’s not likely to lead to lower prices.
Finally, I’m worried there isn’t enough product to meet increased demand. Some suppliers are already working on allocation for insulation and, with demand doubling or trippling per house, the supply chain will not keep up.
Firm: Quality Construction
Interviewee: Dan Albert
Role: Director
Location: Wellington
Staff: 5
We considered the change for some time and six months ago we told our designer to use the new standards. We took into account the cost and practicalities of embracing the new standards, which included speaking to our aluminium joiners to make sure we only use products that will still be the best in five to seven years.
From my point of view, I don’t want to be installing anything that won’t be up-to-date in six months’ time. For me, it doesn’t make sense – I want to jump ahead and lead the industry!
We use R7 insulation and I’m not seeing any issues getting the product and the same goes for our aluminium joinery product but, as we’re a small company, we don’t have to purchase a lot of stock.
As far as cost goes, it will increase the cost of a build but I don’t think it’ll go up by more than 1.5%. When we’re working with contingencies of up to 20%, it shouldn’t hurt the business financially.
Register to earn LBP Points Sign in