Building safety into the process
22 Feb 2014, Community & Sponsorship
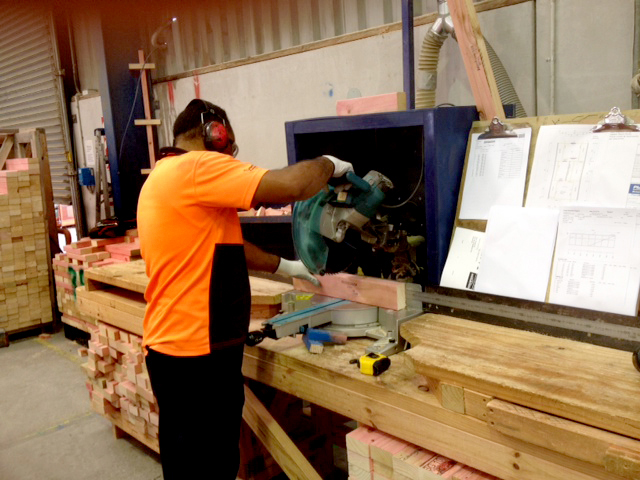
Auckland Frame & Truss creates innovative and effective method for reducing dust exposure. Keen to ensure its Frame & Truss (F&T) plants adhered to new Workplace Exposure Standards (WES) for dust, Auckland Frame & Truss (AFT) took the initiative to build its own solution.
“At AFT, results from our dust exposure testing were consistently within the previous mandated WES,” says national Frame & Truss manager Robert Grimmer. “However, when MBIE announced the allowable levels would be reduced by half, we decided to stay ahead of the regulations and carry out further testing to assess our adherence to the new limits.
“Despite using industry standard extraction – a portable dust extractor attached to a single extraction port – one of the operators’ exposure was 2.882.00mg/m3 air, well over the new 2.00mg/m3 air limit, though well within the previous standard,” says Robert.
“It appeared that the spinning of the saw blade disrupted the air flow to the extraction port, thereby reducing the effectiveness of the extractor.”
Based on these findings, Laurie Smith and John Daniels came up with the design and built a new hood for the saw after working with Massey University and MBIE. It collected the dust as it was becoming airborne and allowed the addition of a second extraction port to remove it. Though a simple design and only $60 to build, the results were impressive.
“Dust exposure levels on the saw with the hood attached were reduced by 80% and were 75% below the new allowable WES,” says Robert.
“Given PlaceMakers’ ten F&T plants across the country process approximately 65,000 cubic metres of timber annually, it’s essential that our staff’s levels of dust exposure are as low as possible and this is a great step in that direction.”
PlaceMakers plans to roll out the these hoods to all F&T plants.
Register to earn LBP Points Sign in