Sharing solutions for H1 changes
14 Oct 2022, News, Product Focus
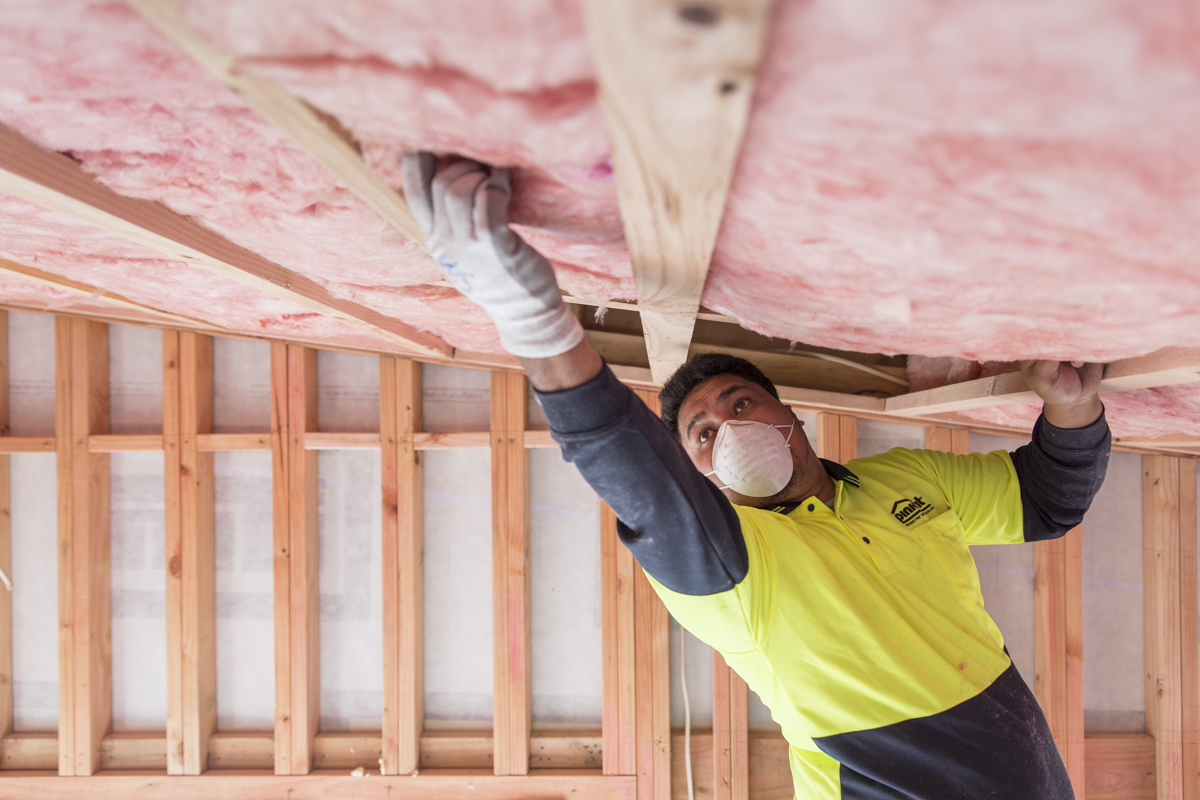
With the biggest energy efficiency changes to the Building Code in over a decade only six months away, PlaceMakers is committed to helping builders navigate the changes as painlessly as possible. To this end, our Glasswool insulation supplier Comfortech® reviews the changes to insulation and provides possible solutions to help builders comply with new ceiling and wall requirements
On 29 November 2021, the Ministry of Business, Innovation and Employment (MBIE) released the biggest energy efficiency updates to the acceptable solutions and verification methods in more than a decade.
H1/AS1 Acceptable Solution changes include increases to ceiling, window, wall and underfloor insulation requirements and introduce six new climate zones to reflect the specific weather experienced in different parts of New Zealand.
Originally the changes were scheduled to come in from 3 November 2022. However, following a consultation, MBIE extended the time to comply with new wall, floor and ceiling insulation requirements in new homes by a further six months, to 1 May 2023.
Changes in insulation requirements will affect residential and small buildings, as well as large buildings. In this article, we focus on small buildings.
In residential and small buildings, MBIE is proceeding with changes to the schedule method for ceiling, window, wall and underfloor insulation requirements, which aim to reduce the energy needed for heating residential homes by approximately 40% over previous minimum requirements.
New climate zones
In recognition of New Zealand’s very different climates, MBIE is expanding the number of climate zones used in the insulation requirements from three to six. This will allow the insulation requirements to better reflect the different climates experienced in each zone. The new climate zones follow territorial authority (local government) boundaries.
There is no one size fits all solution; there are several compliance pathways. Accordingly, the house orientation, the slab insulation, size and type of your windows and wall insulation and ultimately your ceiling insulation will determine the best solution to meet the new H1 requirements for insulation.
Under the schedule method, the minimum is now R6.6 for the ceiling in all climate zones. However, there is an allowance for less insulation around the perimeter in ceilings where space restrictions don’t allow the full thickness of insulation to be installed.
R-value calculation
The Schedule Method has been the traditional method of compliance with H1 for most houses. It involves selecting R-values from a table.
Builders may find their designer has used the Calculation Method , which addresses heat loss from buildings more holistically. It can be used on buildings with up to 40% glazed wall area. It doesn’t, however, address heat load in summer – including the impact of solar gain from glazing and mitigation from shading – or the contribution of thermal mass.
The Modelling Method is the optimum method of compliance. It addresses energy use to deliver a better performing building, taking into account both summer cooling and winter heating loads.
Comfortech® glasswool ceiling solutions
The traditional single layer segment installation methodology will no longer be able to meet the requirements of the new H1. Segment widths designed to fit between truss chords create a thermal chimney over the structure, allowing heat loss into the ceiling space. As R-values increase and calculations are based on more robust accounts for thermal bridging, the impact of this heat loss cannot be adequately offset.
Comfortech® has developed a single layer solution (pictured above), at 460mm, wide which, when notched and fitted between the truss chords, seals the thermal bridge. This will be available as a Pink® Batts® insulation R7.0 for compliance via the schedule method and other R-values for compliance via the Calculation and Modelling methods; these will include Pink® Batts® insulation R4.5 and potentially Pink® Batts® insulation R5.0 and R5.2, which seem to be common requirements via modelling.
Interestingly, we are seeing a move to a two-layer system, often proposed as two layers of traditional R3.6, but the issue with a two-layer R3.6 are twofold. Firstly, the weight of the second layer will compress the first layer, reducing its thermal performance. Secondly, the over thickness of the first layer above the truss chords creates a channel for air flow that significantly undermines the overall thermal performance.
For the two-layer solution (pictured above), Comfortech® recommends a high-density Pink® Batts® first layer of the same thickness as the height of the truss chords. The second layer is then supplied over width (at 460mm wide), so that when the segments are installed, the thermal bridge is completely closed and the insulation performs as per the modelling.
Under the new H1, the last 500mm of the perimeter of the ceiling insulation can be reduced to R3.3, allowing the insulation to be carried out over the top plates of the wall, while reducing the barrier to air flow from the eave edges. There is, however, still a high risk – particularly in ceilings with a pitch below 30 degrees – of the insulation touching the underside of the ceiling underlay, preventing ventilation of the ceiling space and creating a condensation and mould risk. Therefore, Comfortech® recommends the installation of a roll panel vent over the trusses, under the underlay, to maintain this critical ventilation pathway.
Skillion ceilings pose a unique challenge for achieving the new higher values, particularly via the Schedule Method. Currently, R7.0 insulation with a rafter space of 600mm will not meet the required construction R-value of 6.6. Therefore, Comfortech® recommends a two-layer Pink® Batts® insulation solution for skillion ceilings with a second 1.0 layer (at 40m thickness) installed between the ceiling battens.
Other solutions
There are various solutions from other supplier partners to PlaceMakers and these include Polystyrene from Expol and Panel Insulation from Kingspan.
PlaceMakers plays its part
PlaceMakers is committed to helping educate customers on the upcoming changes, as well as highlighting what our supplier partners are doing to help in this regard. Our aim is to provide you with solutions to meet the new Code and make your life easier!
Keep an eye out for more articles like this – in Under Construction, via email and in store – and make sure to come along to our LBP seminars. We also have a page on our website dedicated to providing helpful resources – placemakers.co.nz/online/h1 .
Register to earn LBP Points Sign in